
SAP Manufacturing Execution System
Get complete control over the manufacturing processes and produce high-quality products.
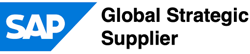
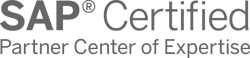
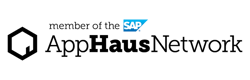
What is SAP Manufacturing Execution System (SAP MES)?
SAP MES is a solution used to manage, monitor, and automate manufacturing operations. SAP MES is suitable for enterprises that require digitizing their production processes and accessing real-time and historical data needed to improve production hall efficiency and optimize manufacturing.
As a system integrator, LeverX cooperates with different hardware providers such as Zebra, Honeywell, and Handheld and offers efficient solutions. We can implement turn-key projects that cover top-of-the-range hardware and software, providing all the necessary equipment from our partners for your warehouse or manufacturing.

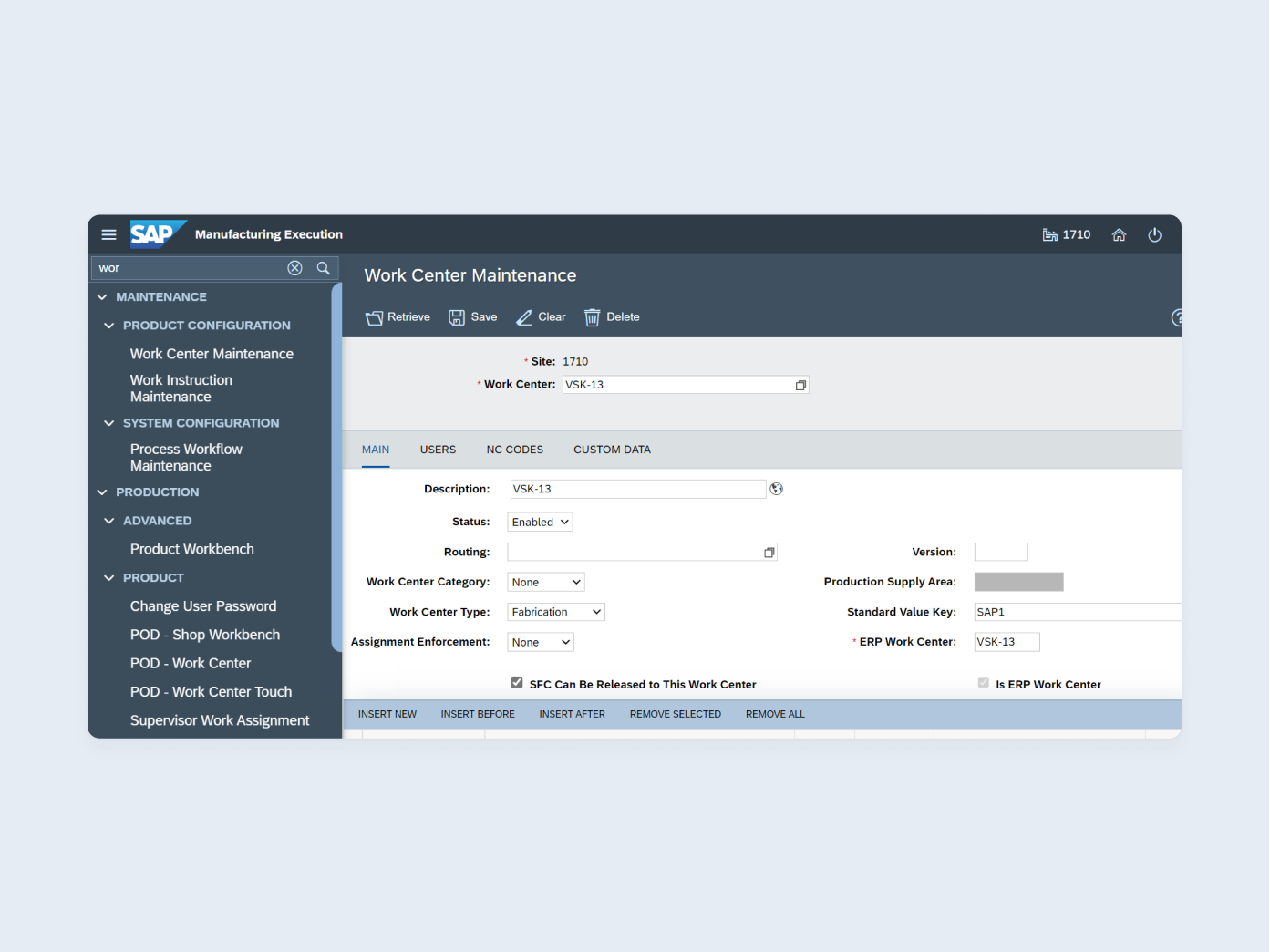
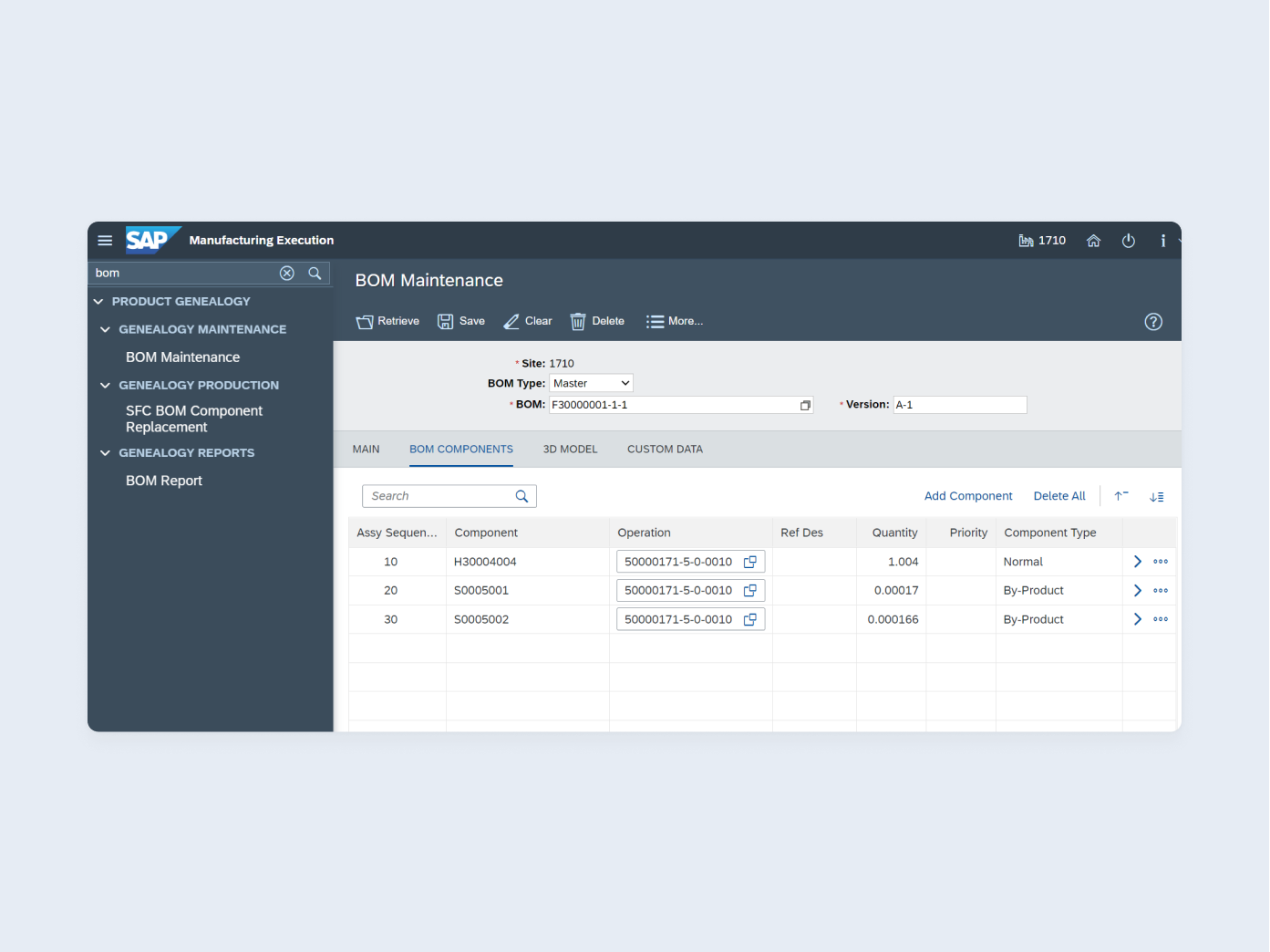
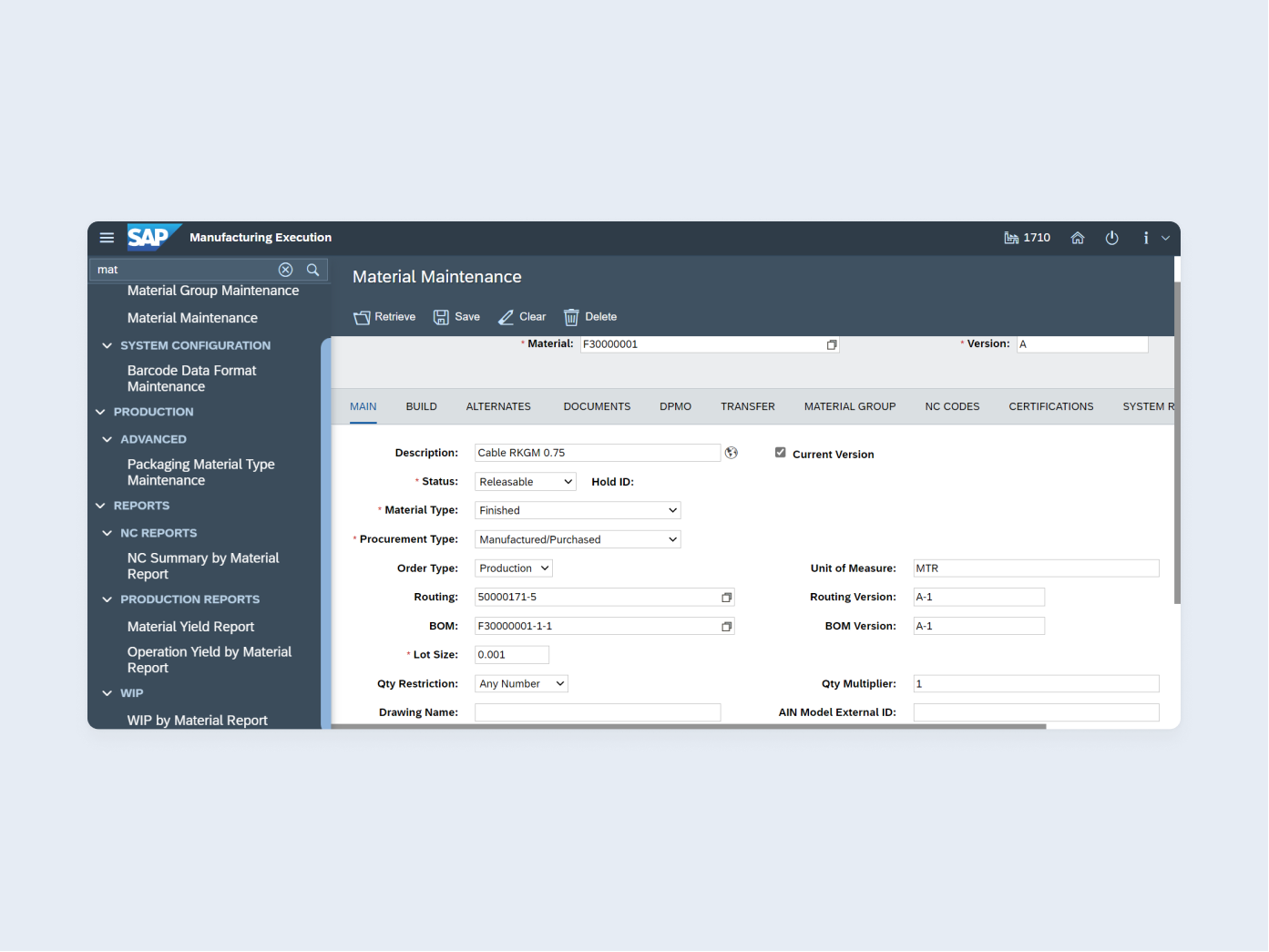
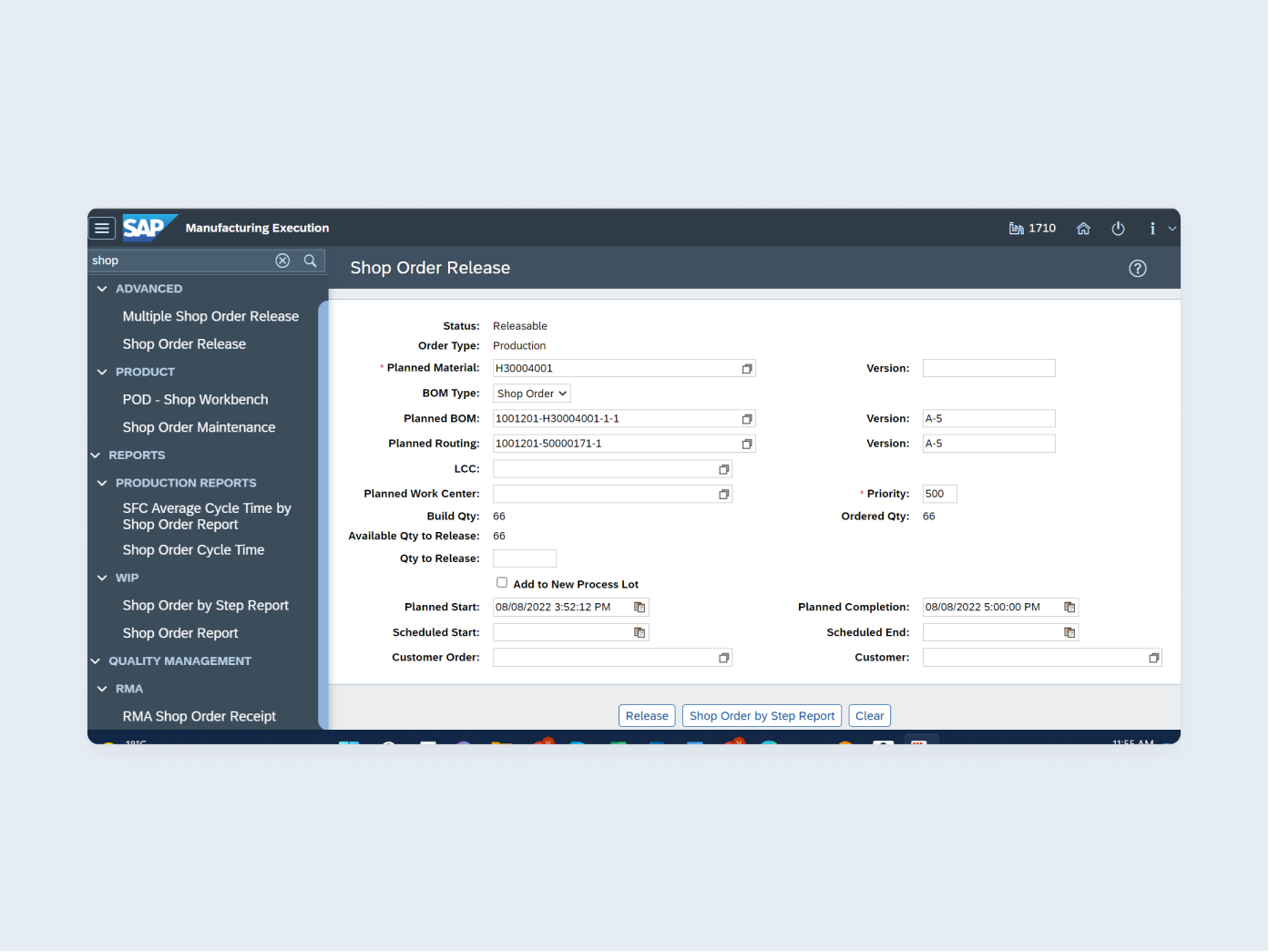
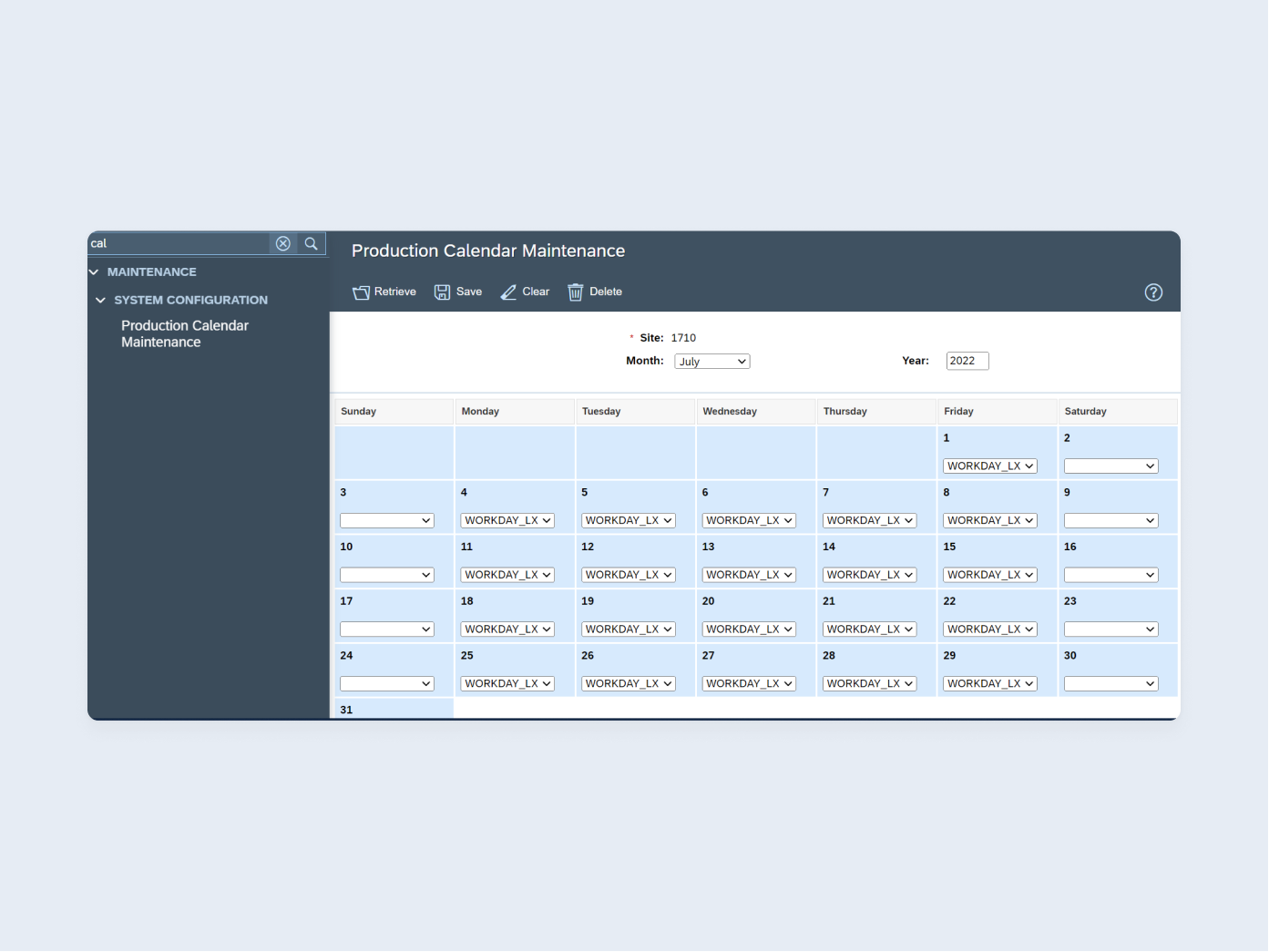
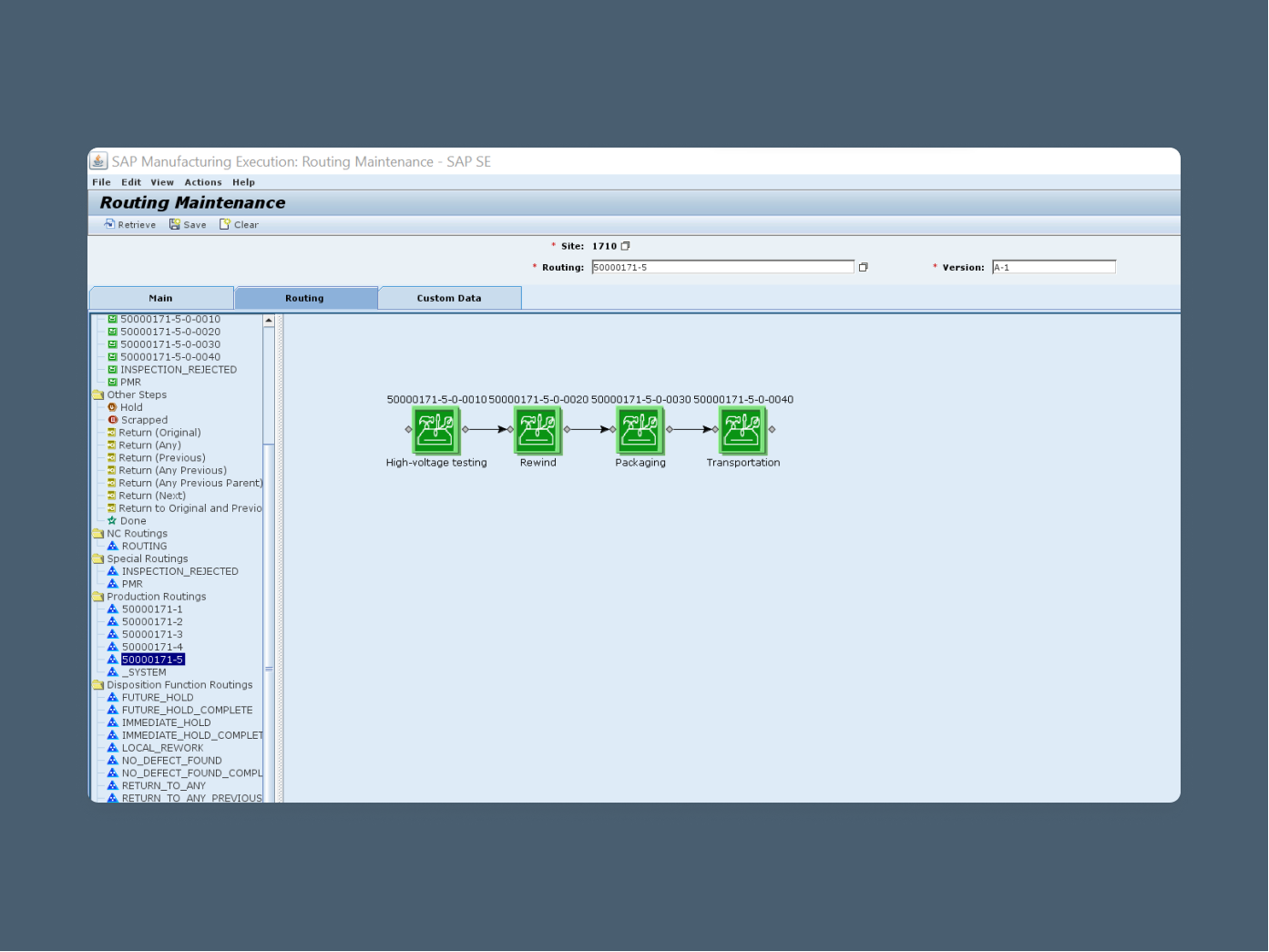
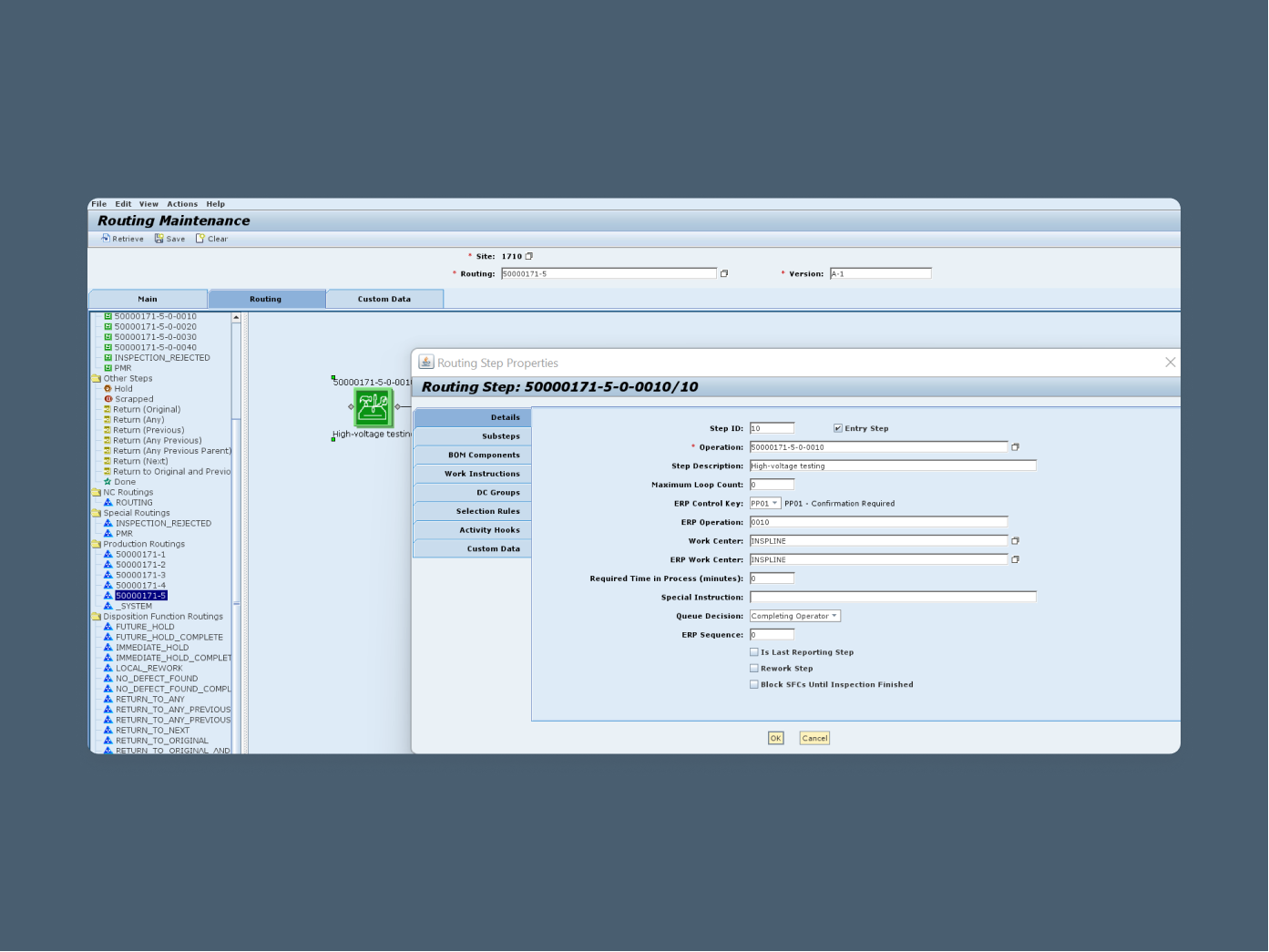
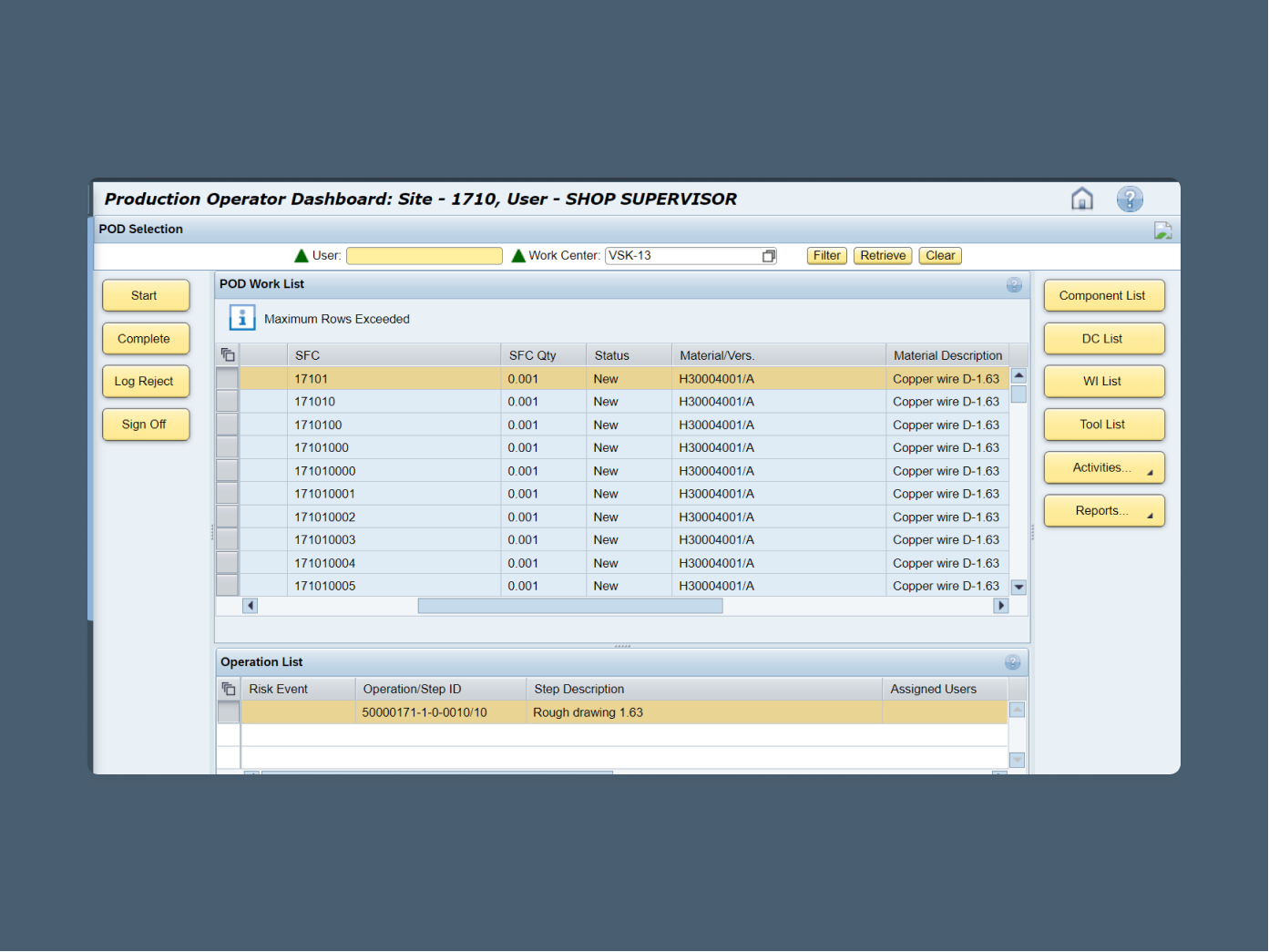
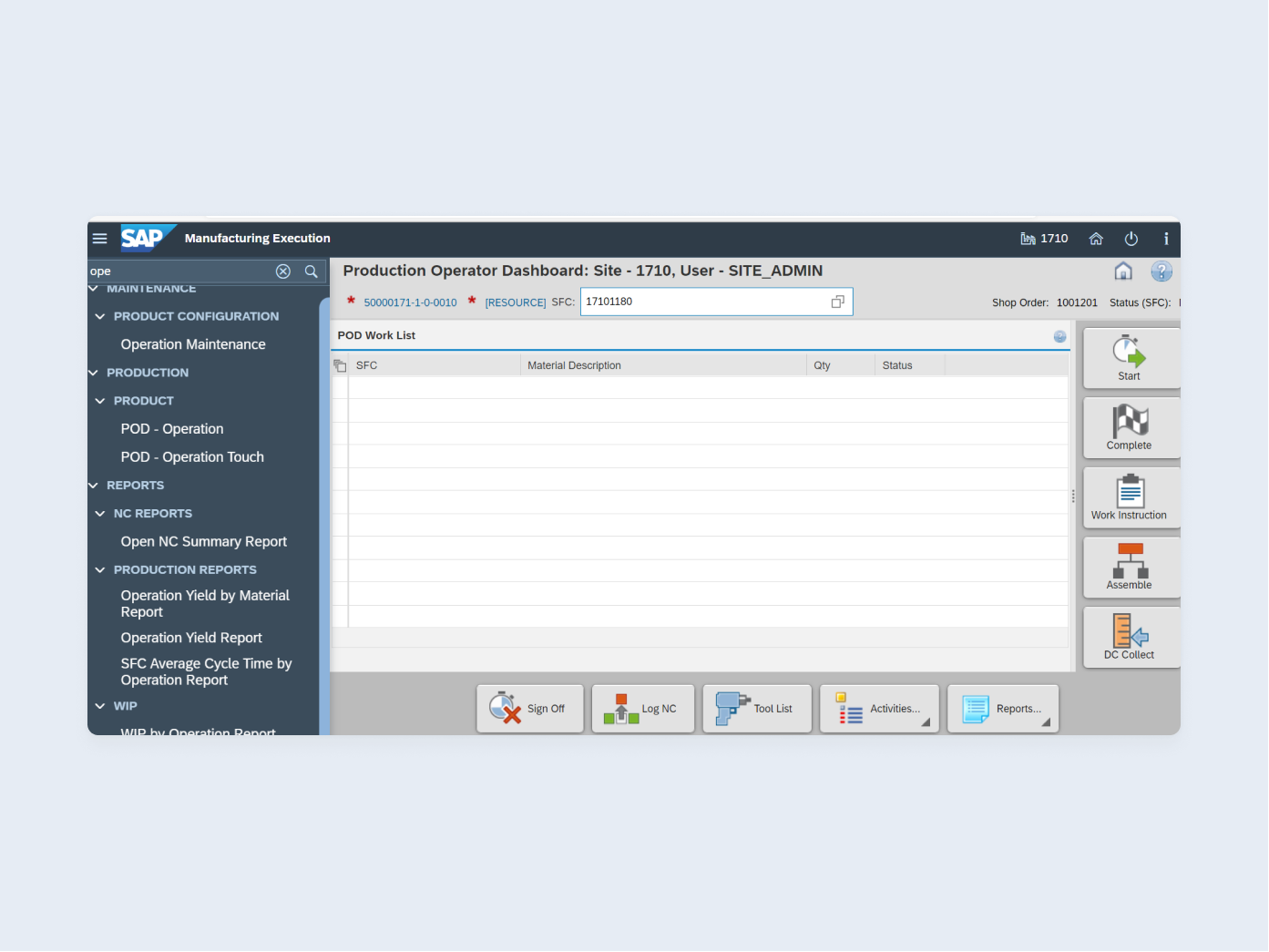
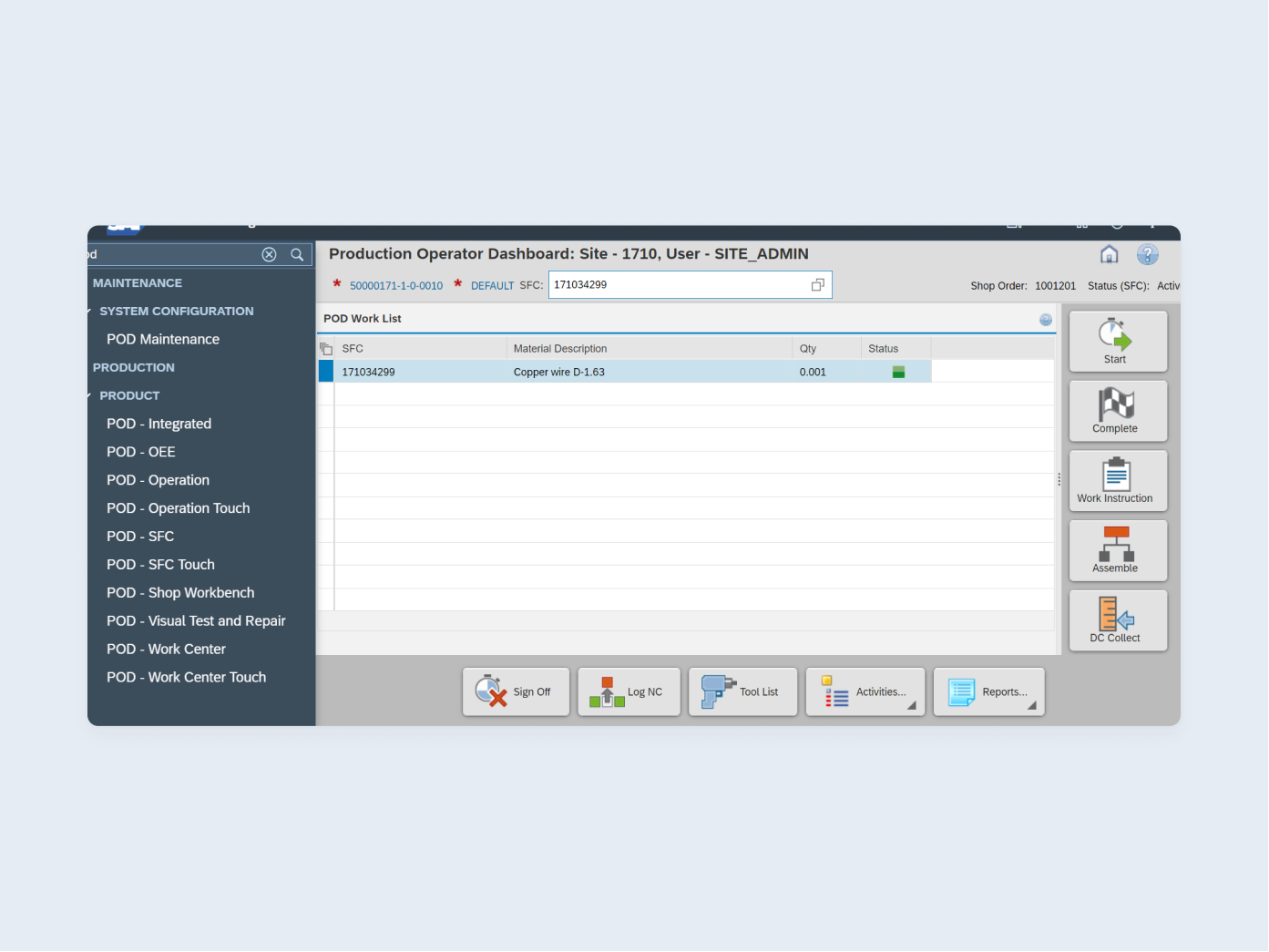
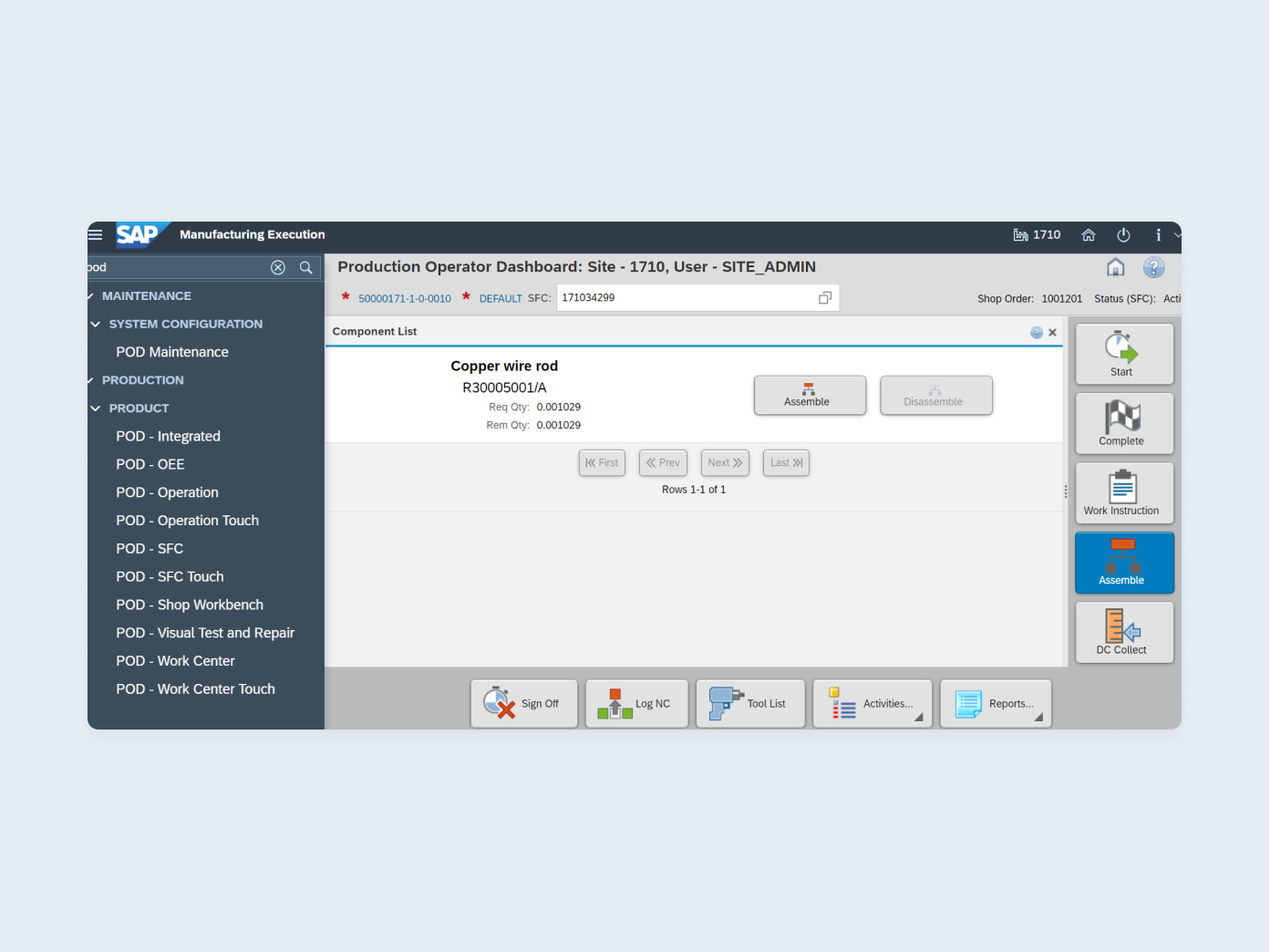
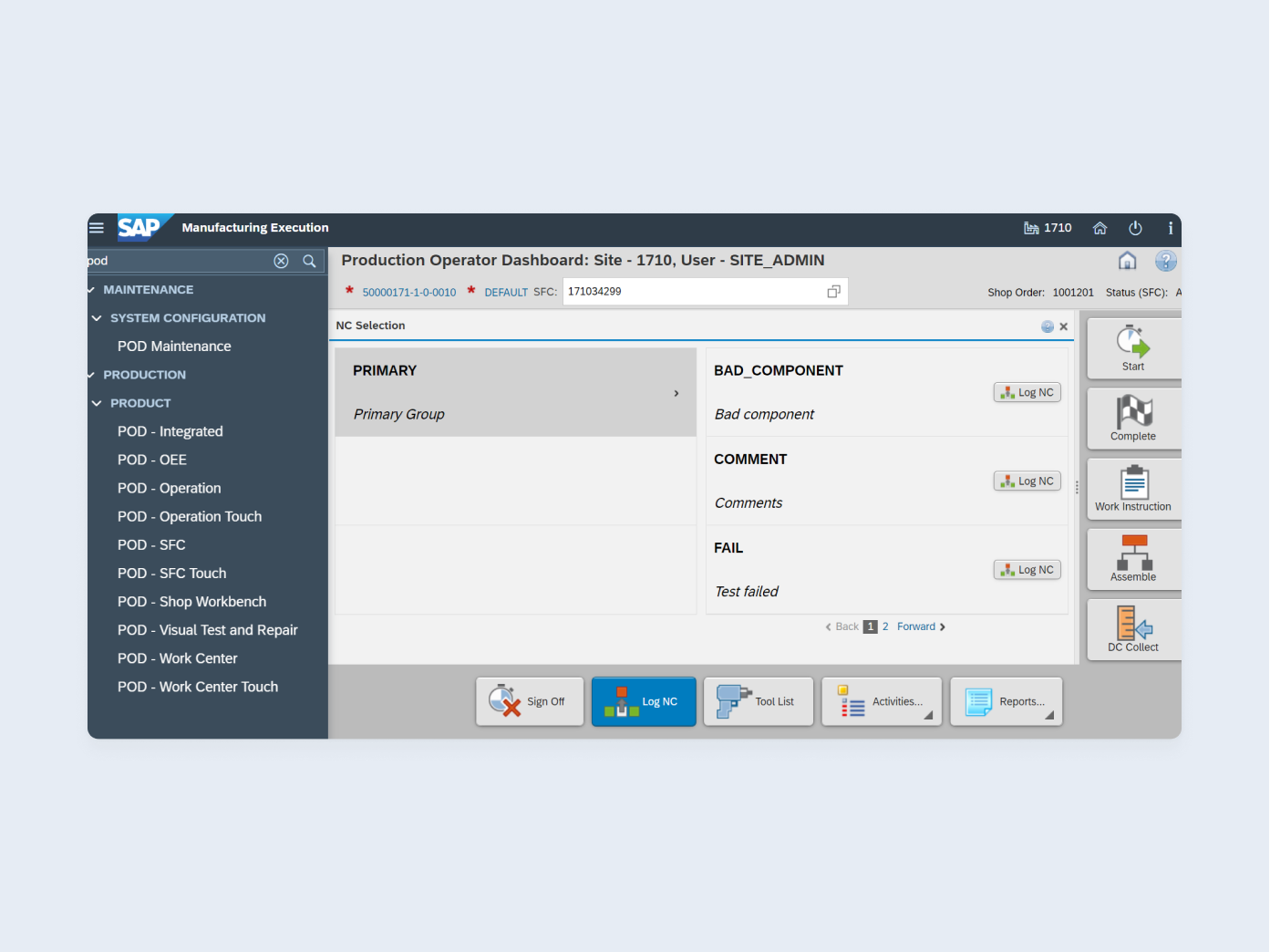
How can SAP MES Help Your Business?
Centralized processes
Real-time data
Genealogy
Product quality improvement
Flexibility
Asset management
What Business Issues Will You Overcome With MES?
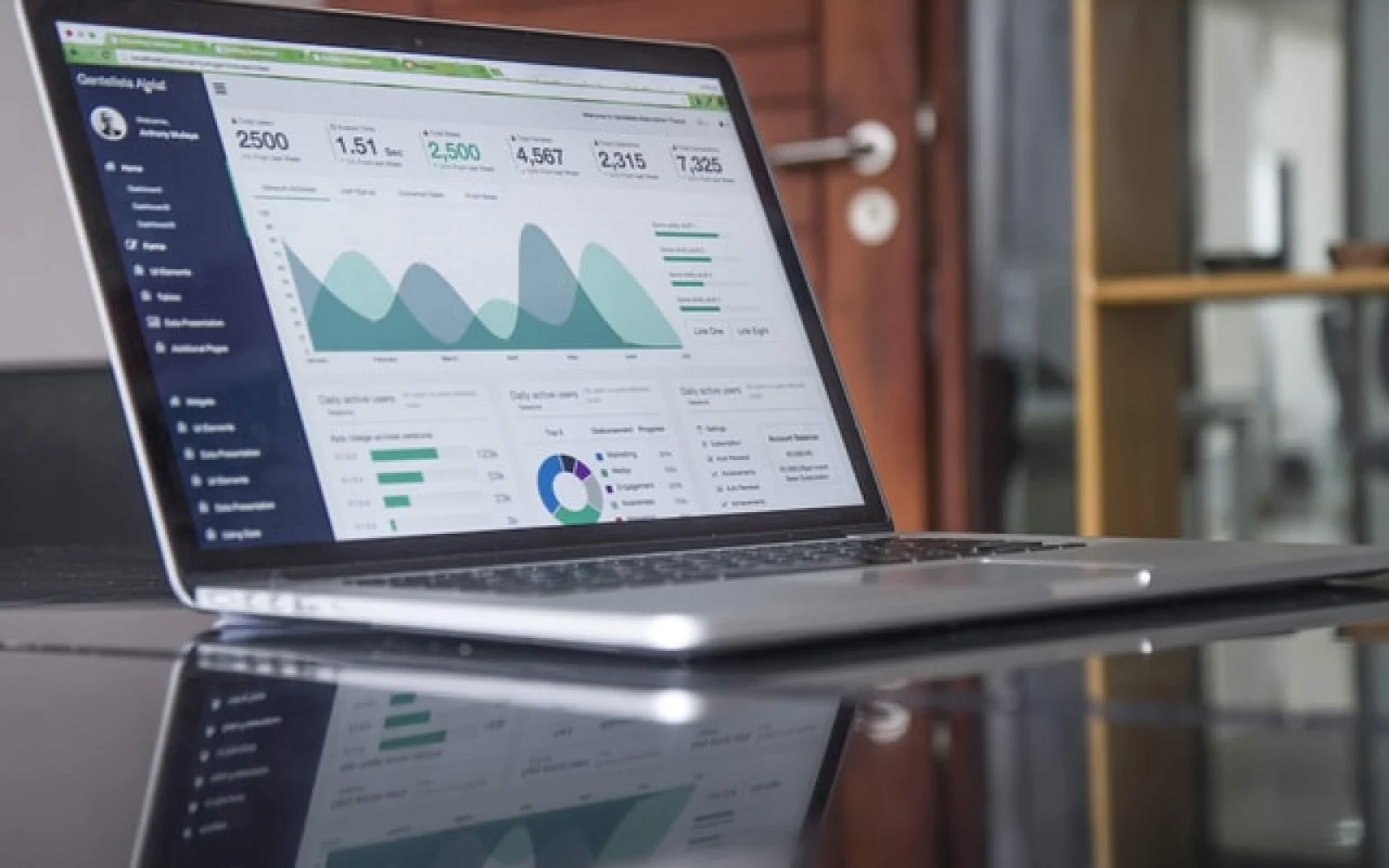
Data Collection
- Track and collect real-time production data
- Data analytics
- Real-time reporting
- Timely transmission of product data to the users involved in the production process
- Instructions view (including 3D format)
- Entire production process view
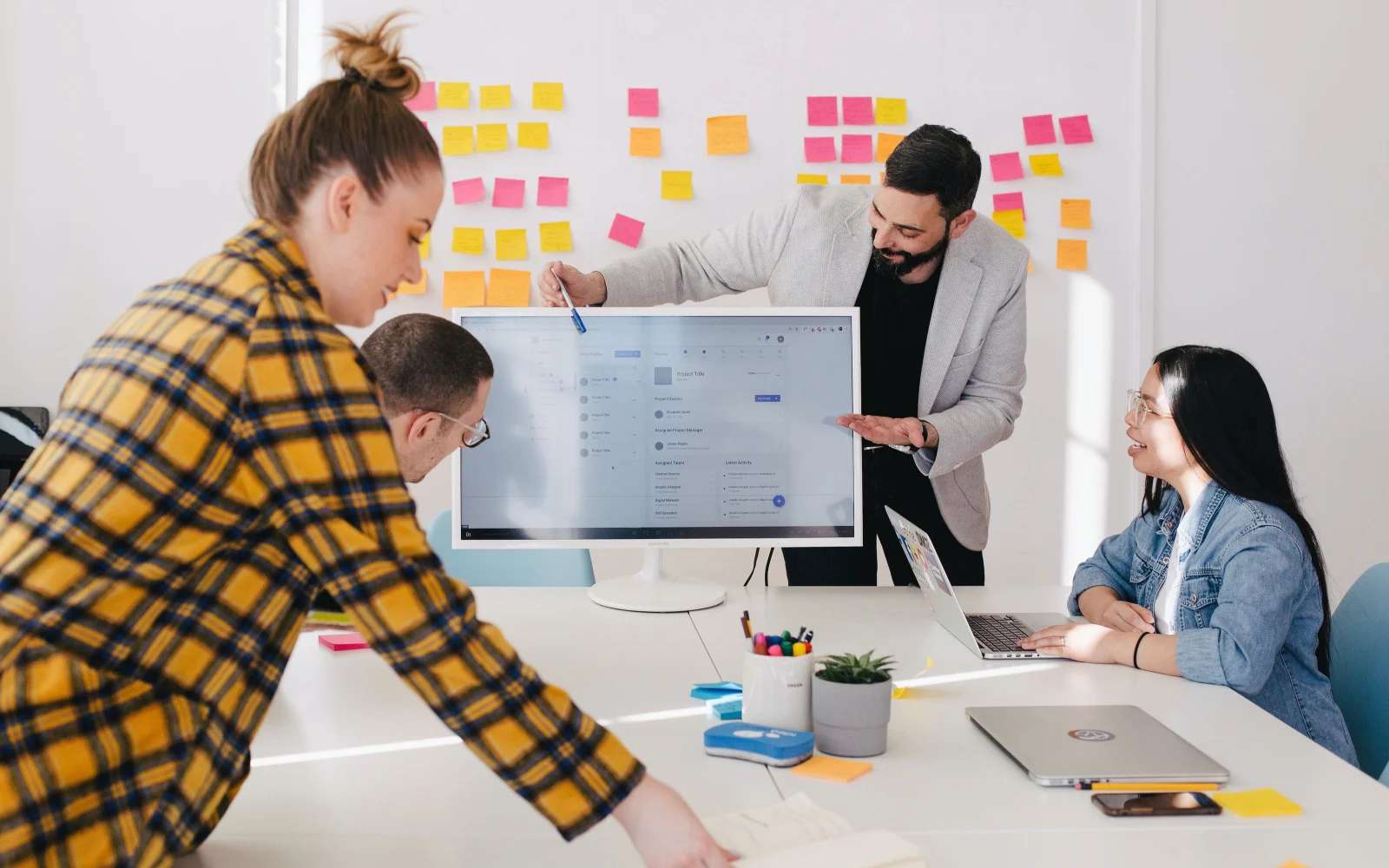
Planning
- Order planning
- Labor scheduling
- Operations scheduling
- Maintenance planning
- Capacity planning
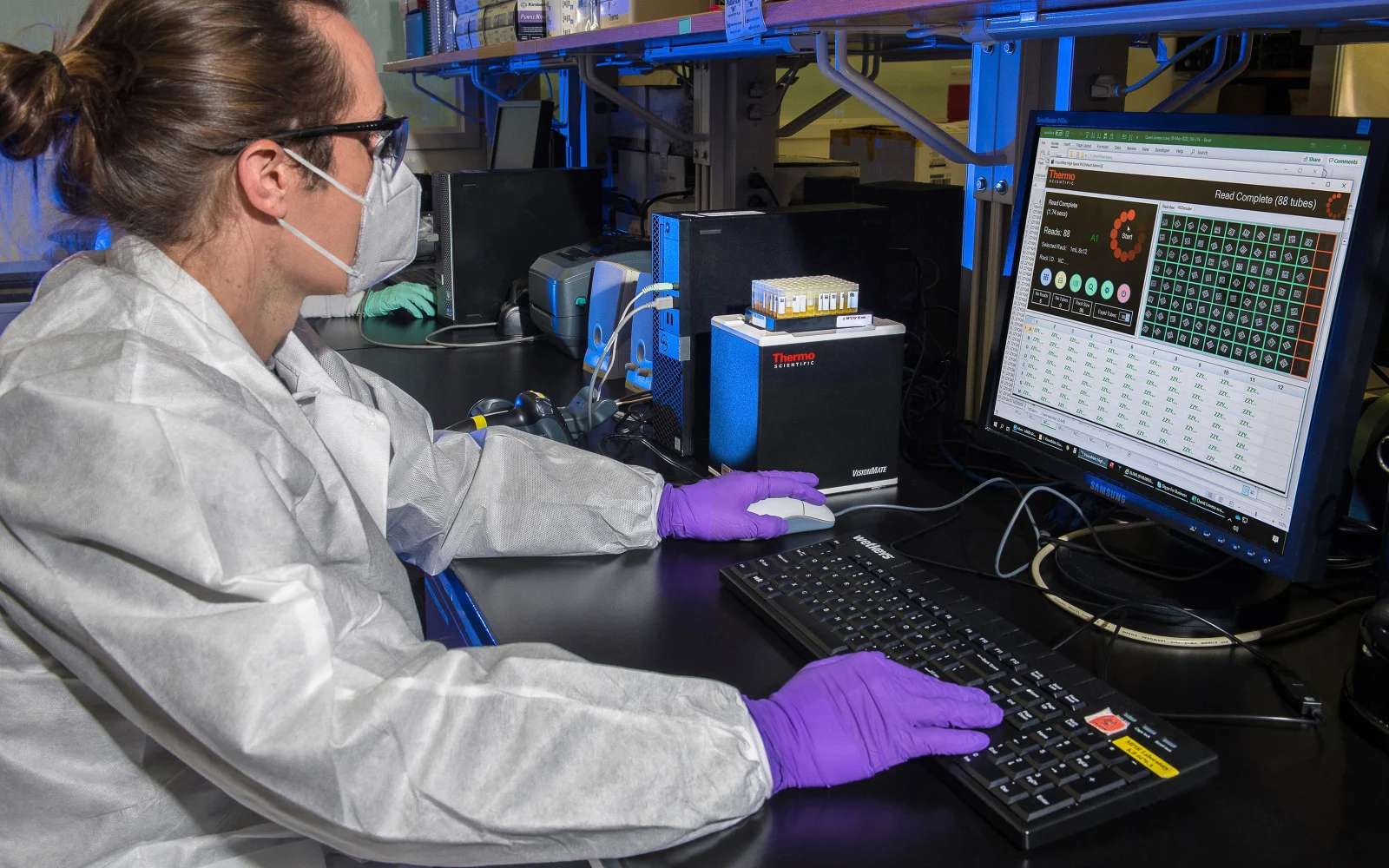
Product Quality Control
- Compliance with product requirements
- Tracking quality deviations and exceptions
- Quality control management
- Documentation management
- Real-time change management
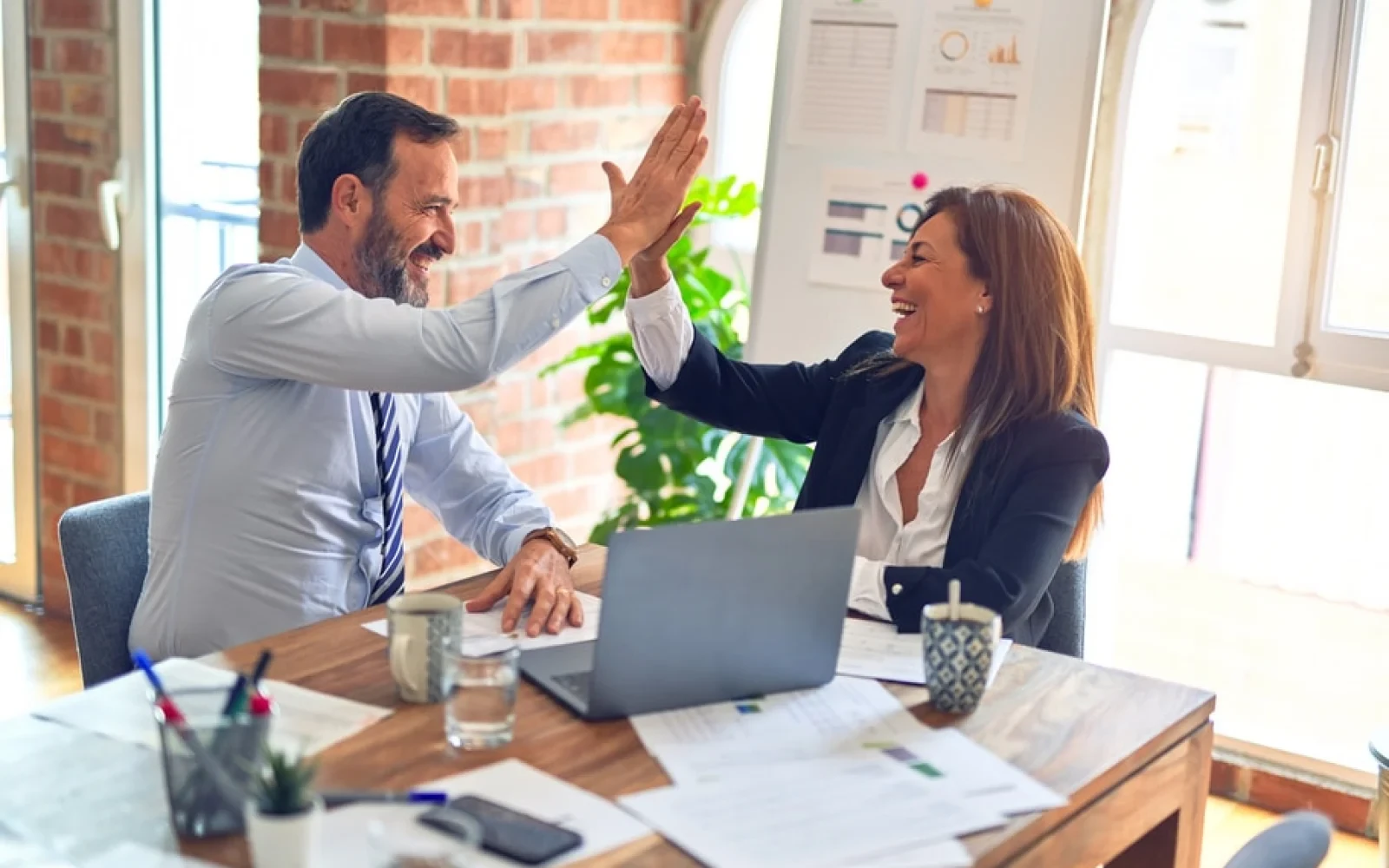
Capacity Management
- Tracking of production facilities efficiency
- Current process visualization
- Controlling and regulating production processes
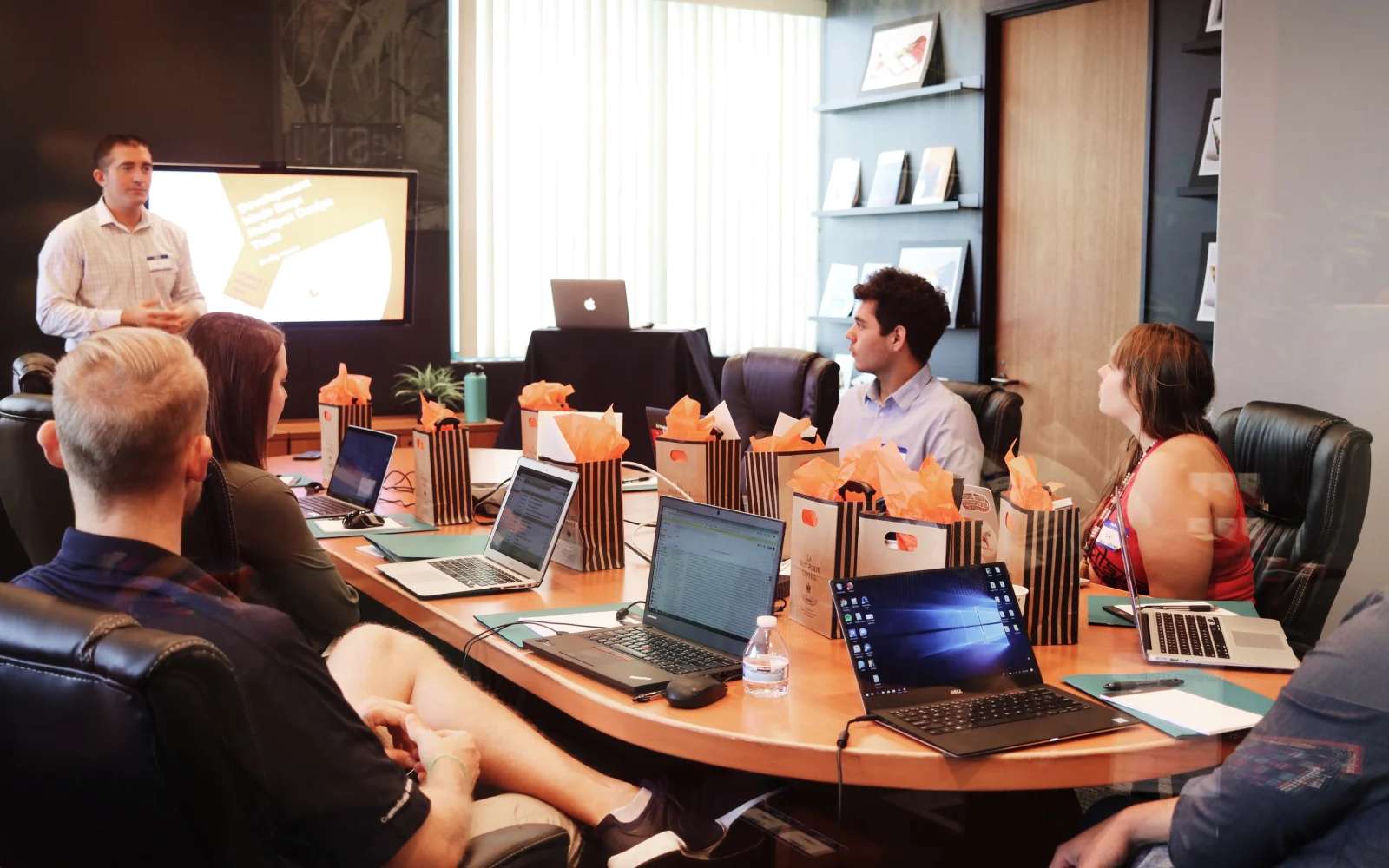
Labor Management
- Tracking worker qualifications
- Shift and personnel scheduling
- Staff time recording
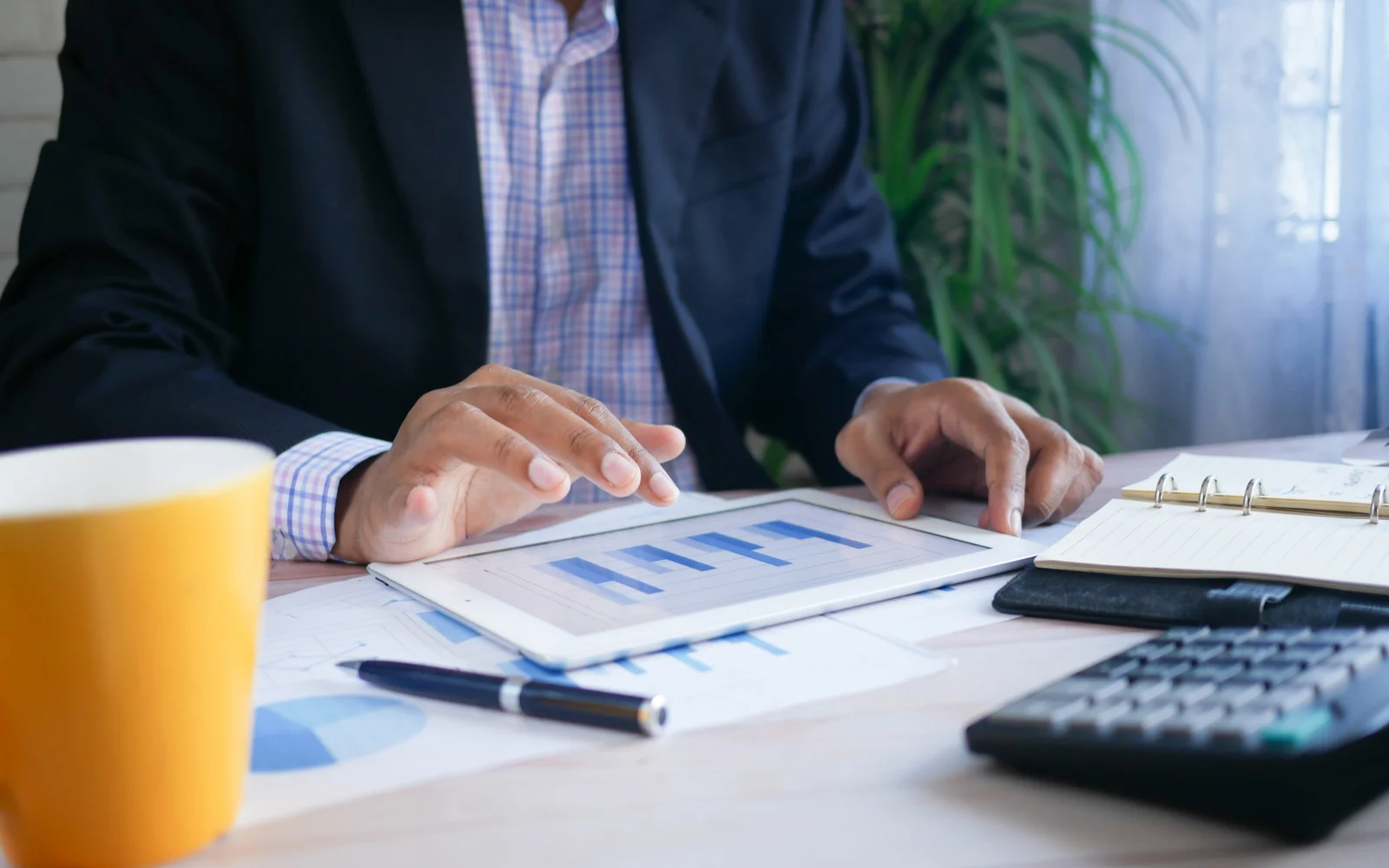
Performance Analysis
- Comparing results and goals to identify strengths and weaknesses
- Key Performance Indicators (KPIs)
- Predictive and prescriptive analyses
- Customized notification and alerts
How Does SAP MES Work?
Order creation by an operator. Production processes accounting
Components and raw materials delivery to production.
Capacity utilization (machines, production lines)
Received production data analysis
Business improvement
Increased profits
How We Can Help
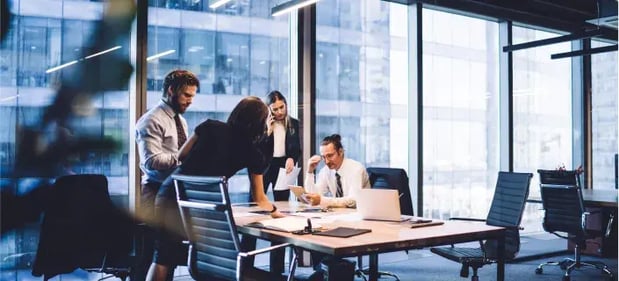
Consulting
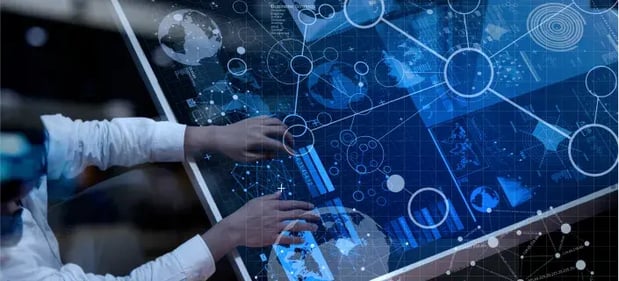
Implementation
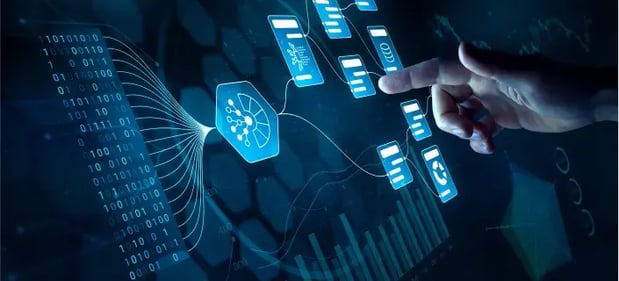
Integration
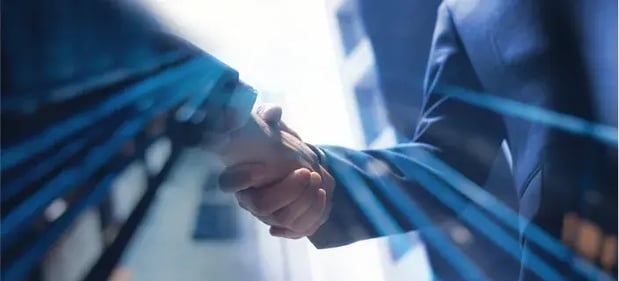
Support
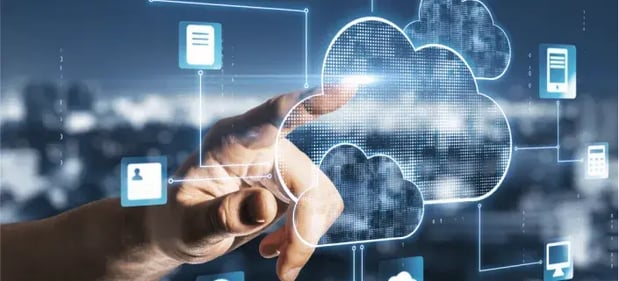
Cloud migration
Customers' success stories
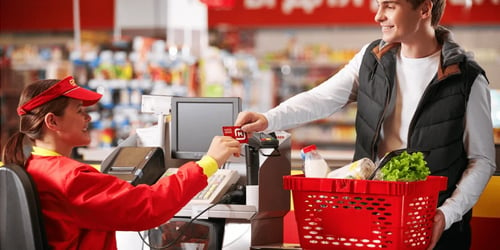
SAP Transportation Management Implementation for a Large Retailer
The LeverX team of experts helped a retail company implement SAP TM, thereby automating transport processes and significantly improving the company's key performance indicators.
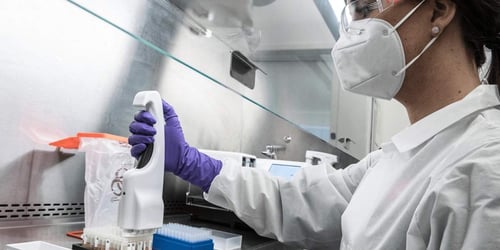
SAP EWM Greenfield Implementation for a Large Manufacturer of Medicines
Thanks to the LeverX team, a customer streamlined warehouse operations and increased material traceability with SAP EWM.
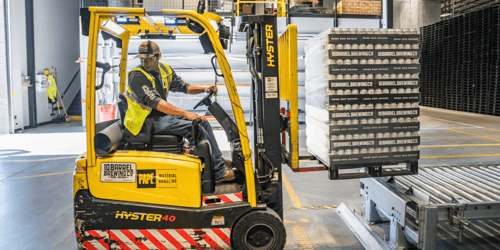
SAP ACM And SAP TSW Integration with SAP TM on SAP S/4HANA for a Manufacturing Provider
Our team was responsible for all integration milestones and the development extensions based on the standard SAP TM objects.
Industries We Serve
Our Partnerships
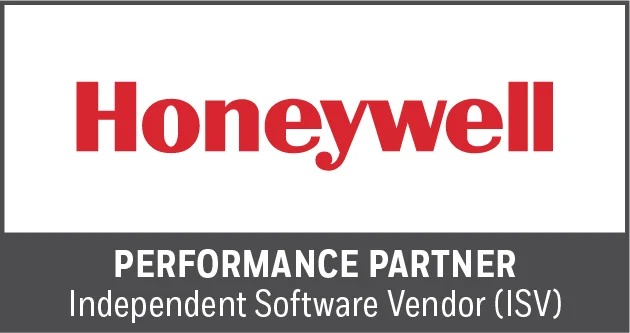
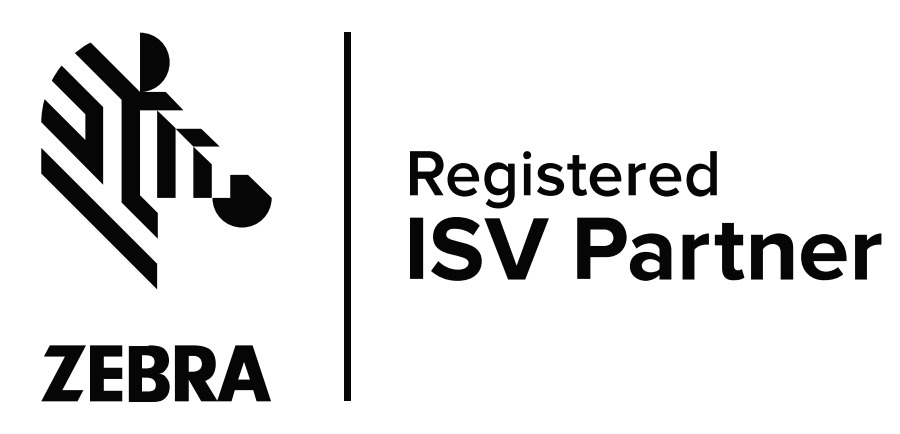
Why Choose LeverX as Your SAP Implementation Provider?
Proven track record
Industry experts
SAP partnership
Quality and security track record
Investment in innovation
Flexibility
Implementation Roadmap
- Current Processes Evaluation: Assess existing business processes and identify the organization's needs.
- Defining Technical Requirements: Create a detailed specification of the functional and technical needs of the new system.
Discover
- Setting Goals and Objectives: Establish and agree on the goals to be achieved throughout the project.
- Assembling the Project Team: Appoint team members and define their roles and responsibilities.
- Project Plan Development: Create a comprehensive plan that outlines project phases, timelines, resources, and key performance indicators.
- Budget Determination: Estimate and approve the budget.
- Specifications Preparation: Develop the technical and functional specifications for the development team.
Prepare
- Ensuring Business Requirements are Met: Check that SAP MES aligns with business requirements and project objectives.
- Data Validation: Verify the accuracy and compliance of the data.
Explore
- Data Migration: Transfer data from existing systems to the new one.
- System Configuration: Set up the solution according to requirements and specifications.
- Customization: Develop additional features and modules, if the standard solution does not meet all needs.
- Integrations: Configure SAP MES to work with other IT systems and applications.
Realize
- Testing: Perform functional, integration, regression, and load testing to ensure that all works correctly.
- User Training: Organize sessions to help users become familiar with the new system.
Deploy
- System Readiness Check: Verify that the system is ready for operational use.
- Launch: Officially transition to active use of SAP MES.
- Ongoing Support: Continuously monitor solution performance to identify and resolve any issues.
Run
FAQ
While both SAP MII and SAP MES are part of SAP's manufacturing solutions, they serve different purposes.
SAP MII focuses on integrating shop floor systems and devices with enterprise applications like SAP ERP or S/4HANA. It enables data collection, analysis, and visualization, providing real-time visibility into shop floor operations.
SAP MES focuses on managing and controlling production processes on the shop floor. It provides functionalities like production order management, quality control, and labor management, enabling efficient execution of production plans.
CONTACT US
If you are looking for an SAP Global Strategic Supplier or Technology Partner for your business, fill out the form below, and we will contact you at short notice.
Contact Us
What happens next?
-
1
An expert will reach out to you to discuss your specific needs and requirements.
-
2
We'll sign an NDA to ensure any sensitive information is kept secure and confidential.
-
3
We'll work with you to prepare a customized proposal based on the project's scope, timeline, and budget.
years of expertise
projects
professionals
Contact Us