
SAP Manufacturing Execution System
Manage every stage of your production process to consistently deliver outstanding product quality.
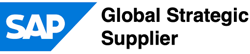
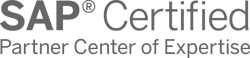
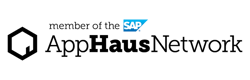
What is SAP Manufacturing Execution System (SAP MES)?
SAP MES is an advanced solution designed to manage, monitor, and automate manufacturing operations. It is well-suited to organisations looking to digitize their production processes and access both real-time and historical data to boost shop floor efficiency and optimise manufacturing performance.
As a system integrator, LeverX partners with established hardware providers such as Zebra, Honeywell, and Handheld to deliver effective solutions. We implement comprehensive, turn-key projects that combine high-quality software with premium hardware, supplying all the necessary equipment from our partners to support your warehouse or manufacturing facility.

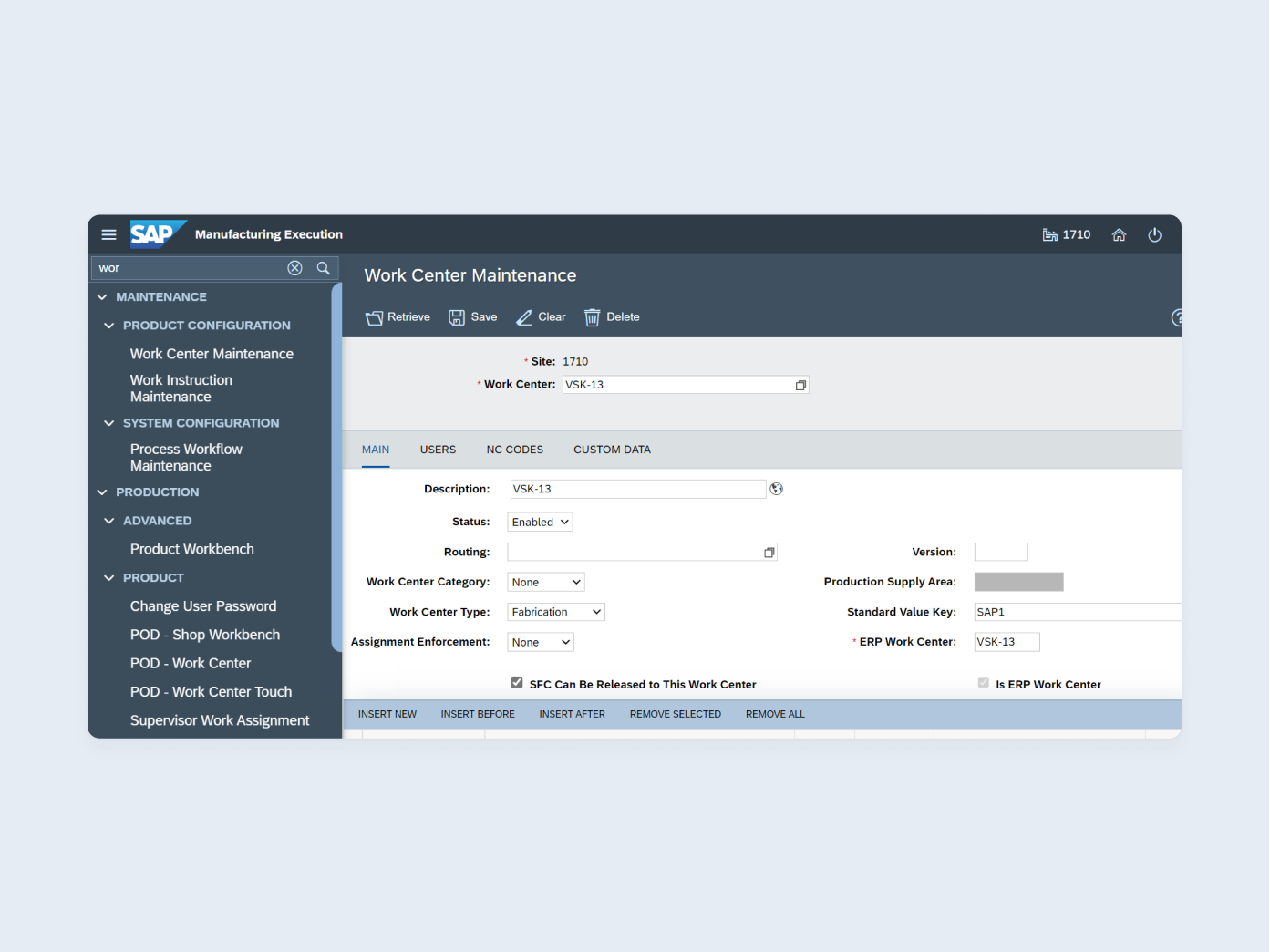
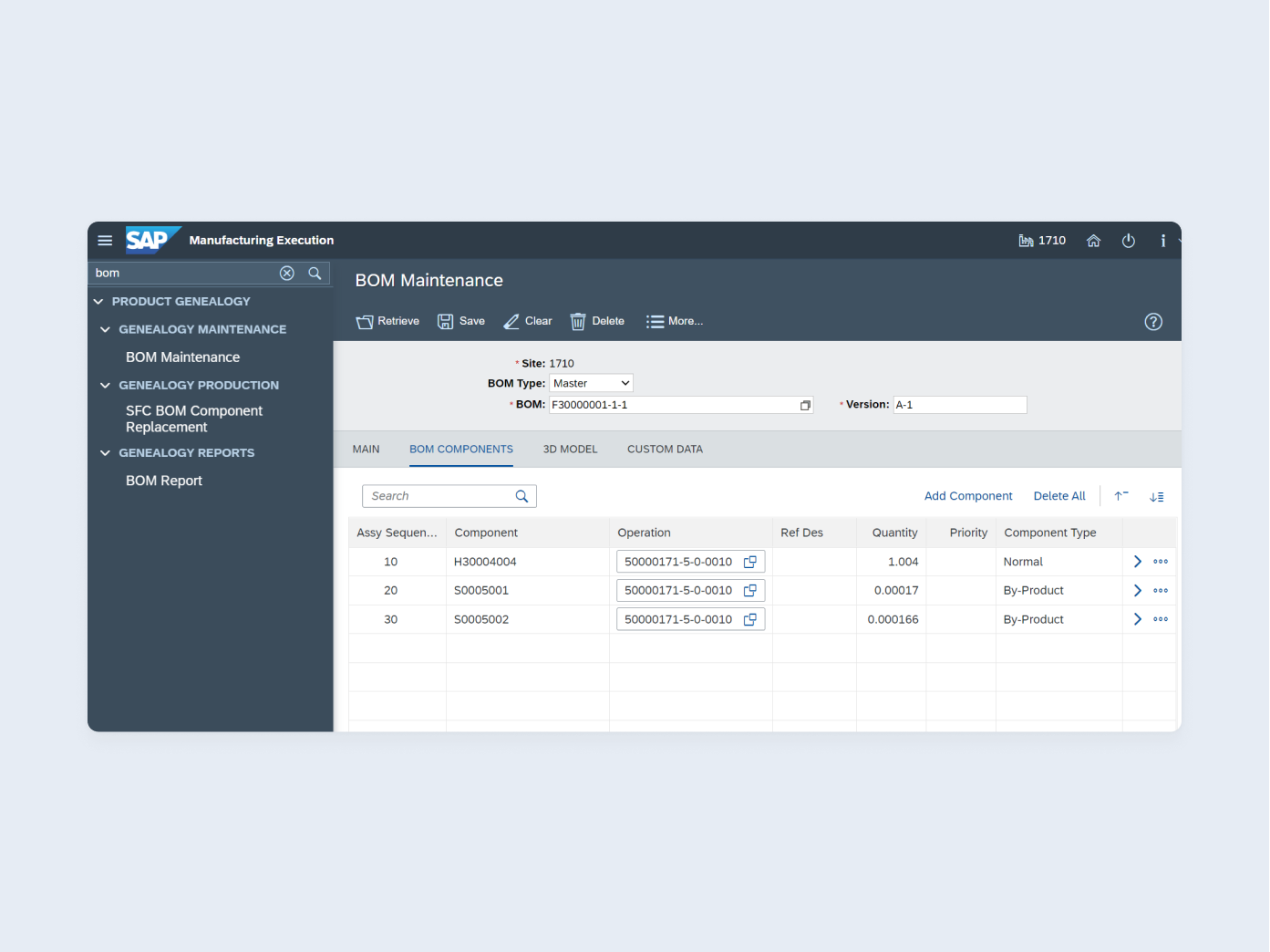
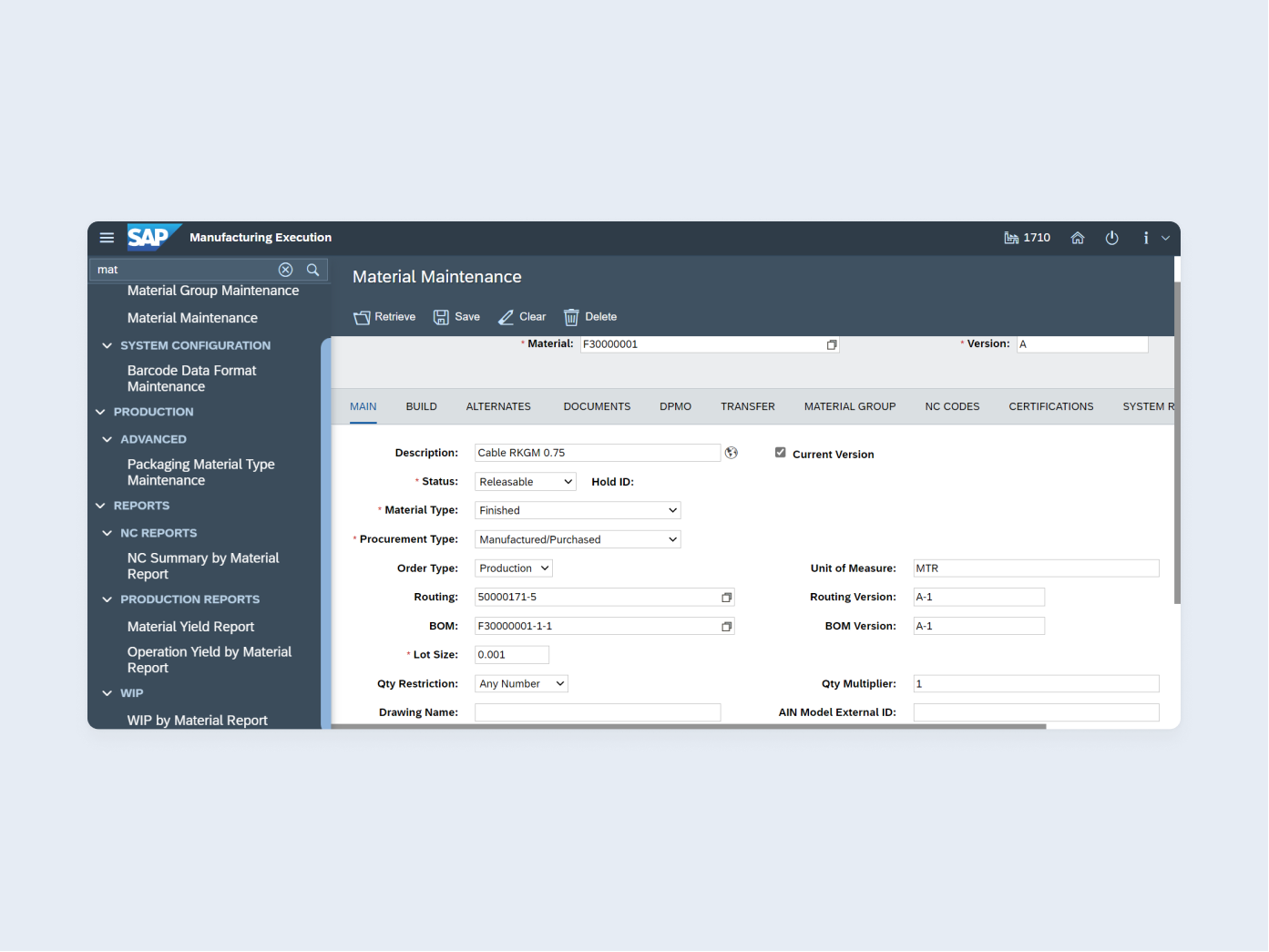
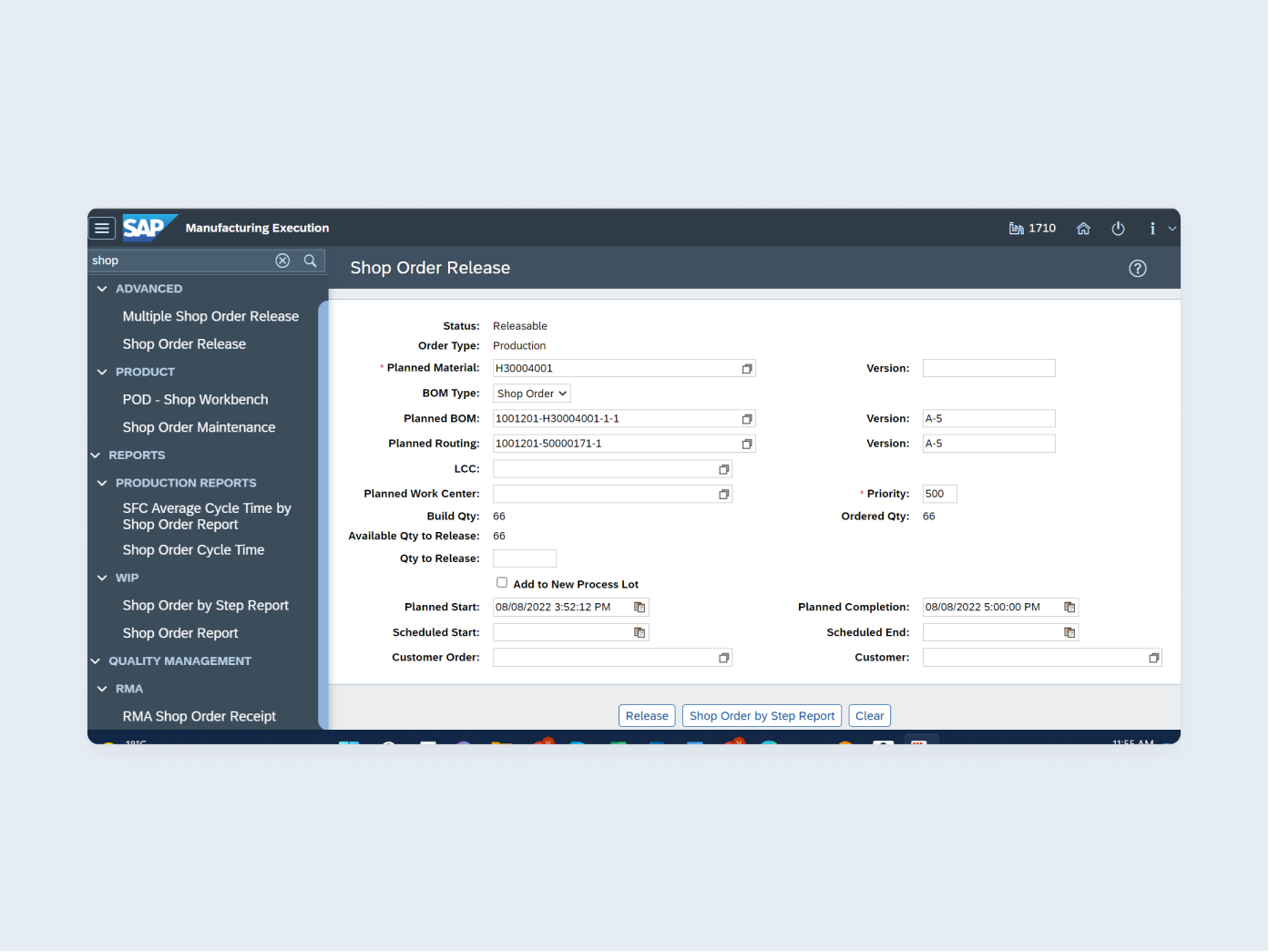
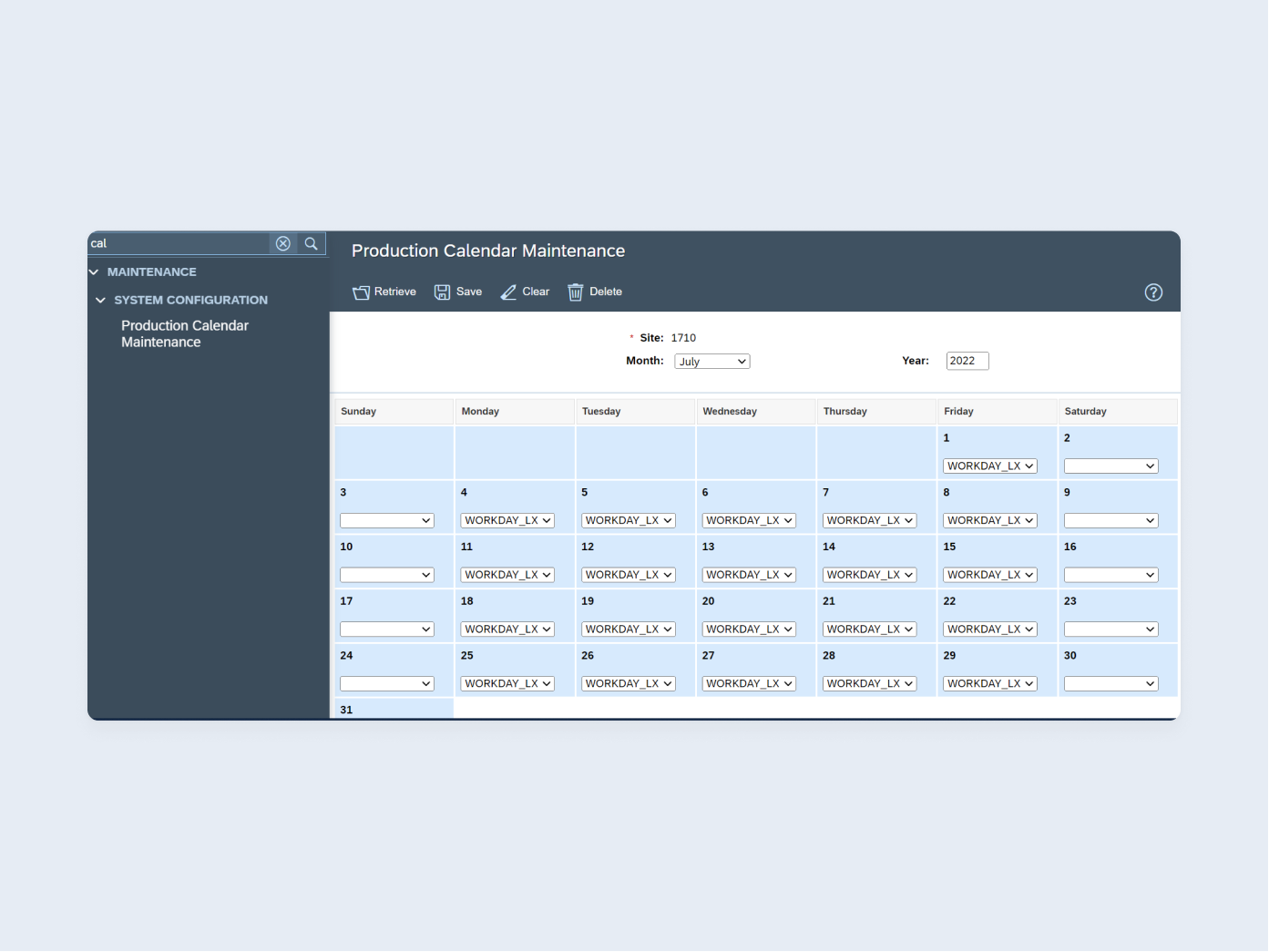
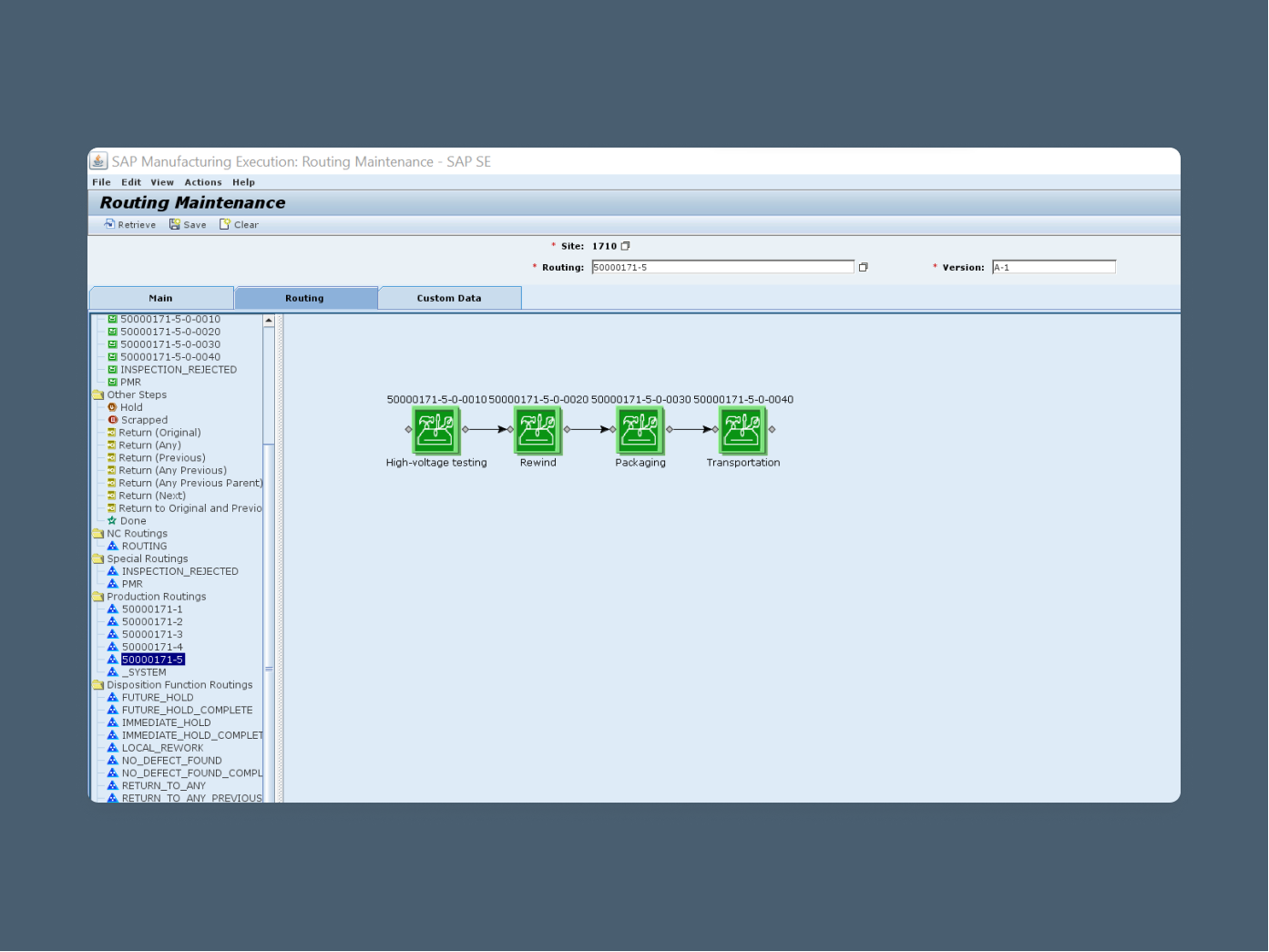
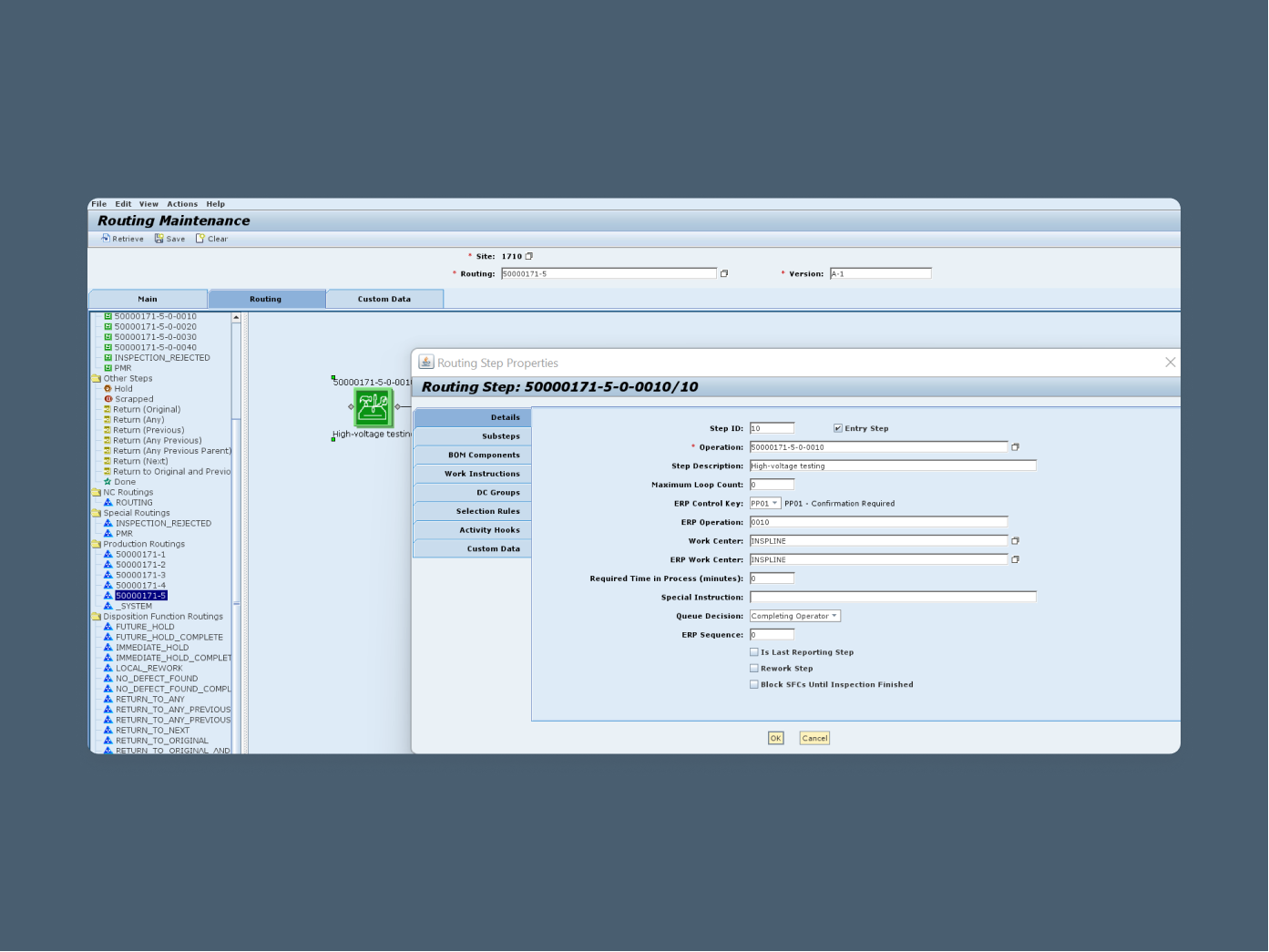
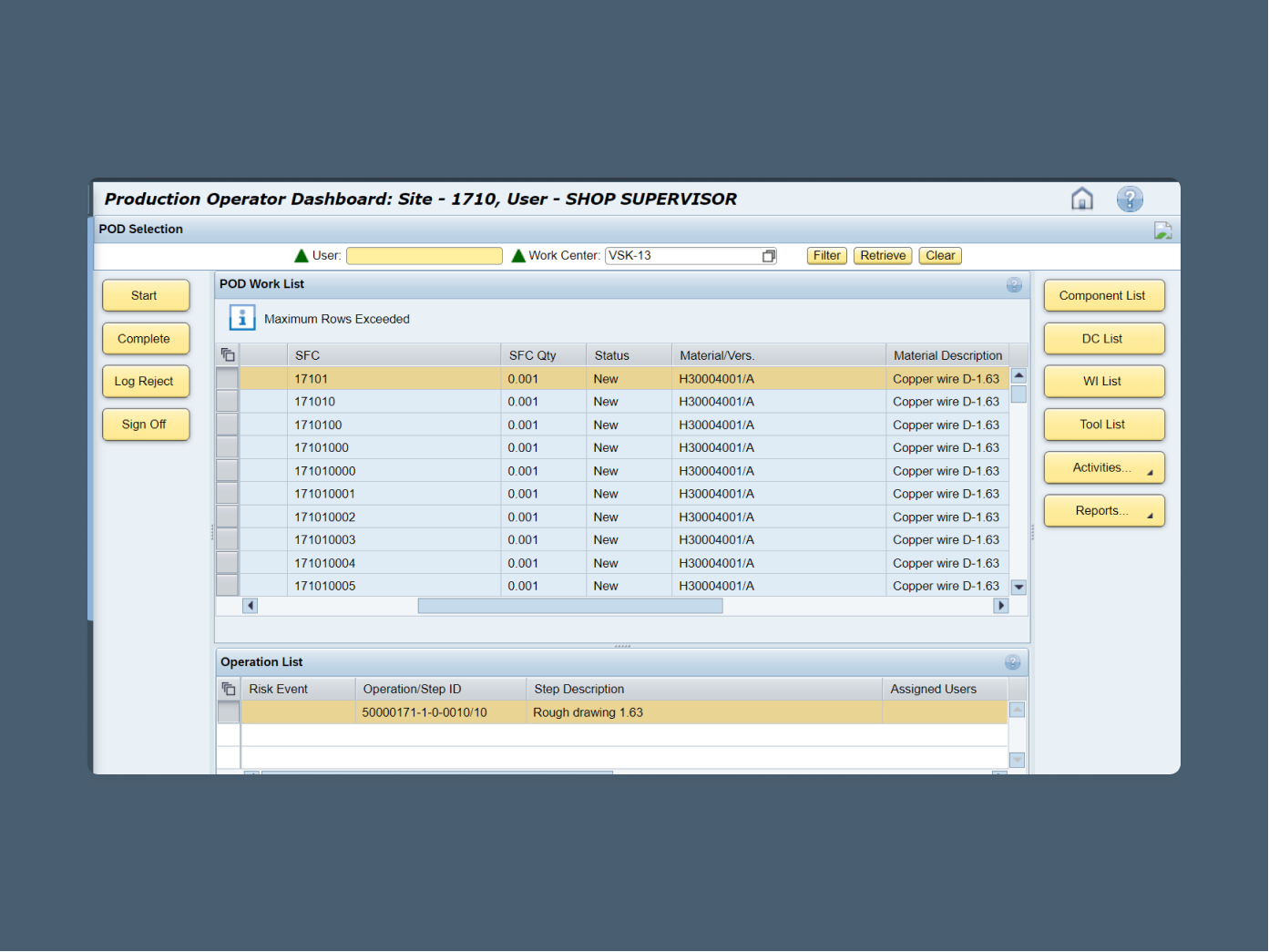
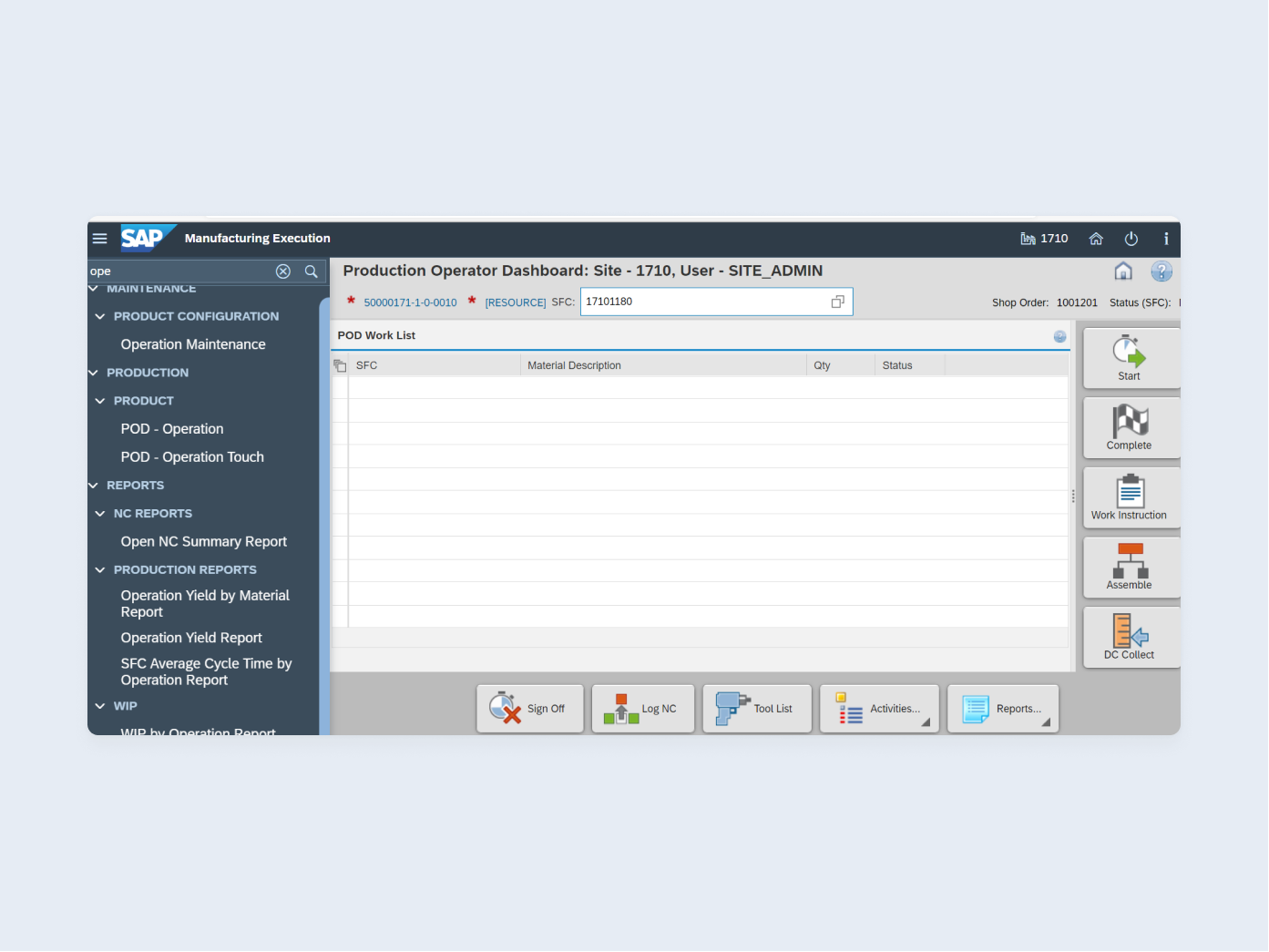
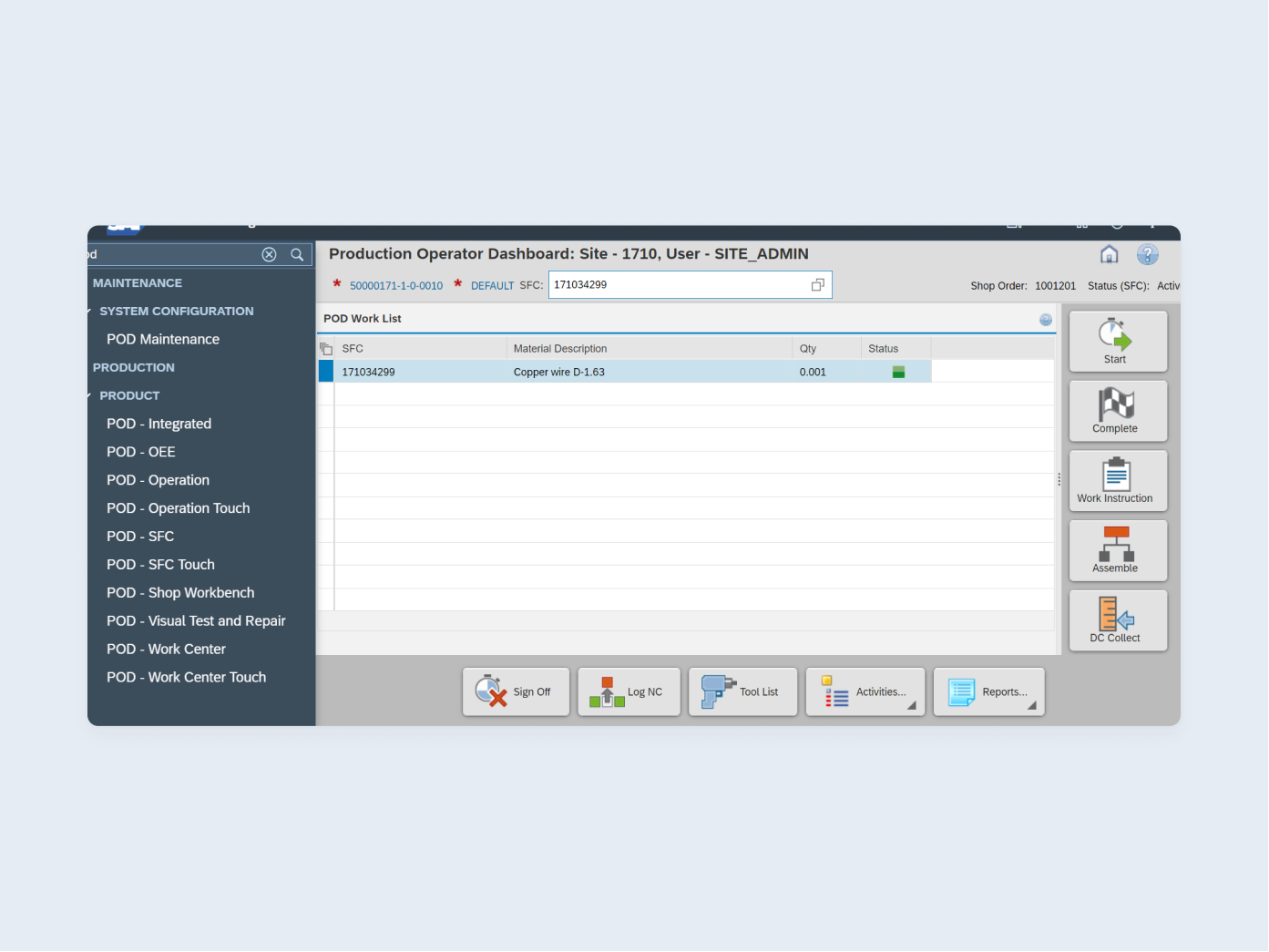
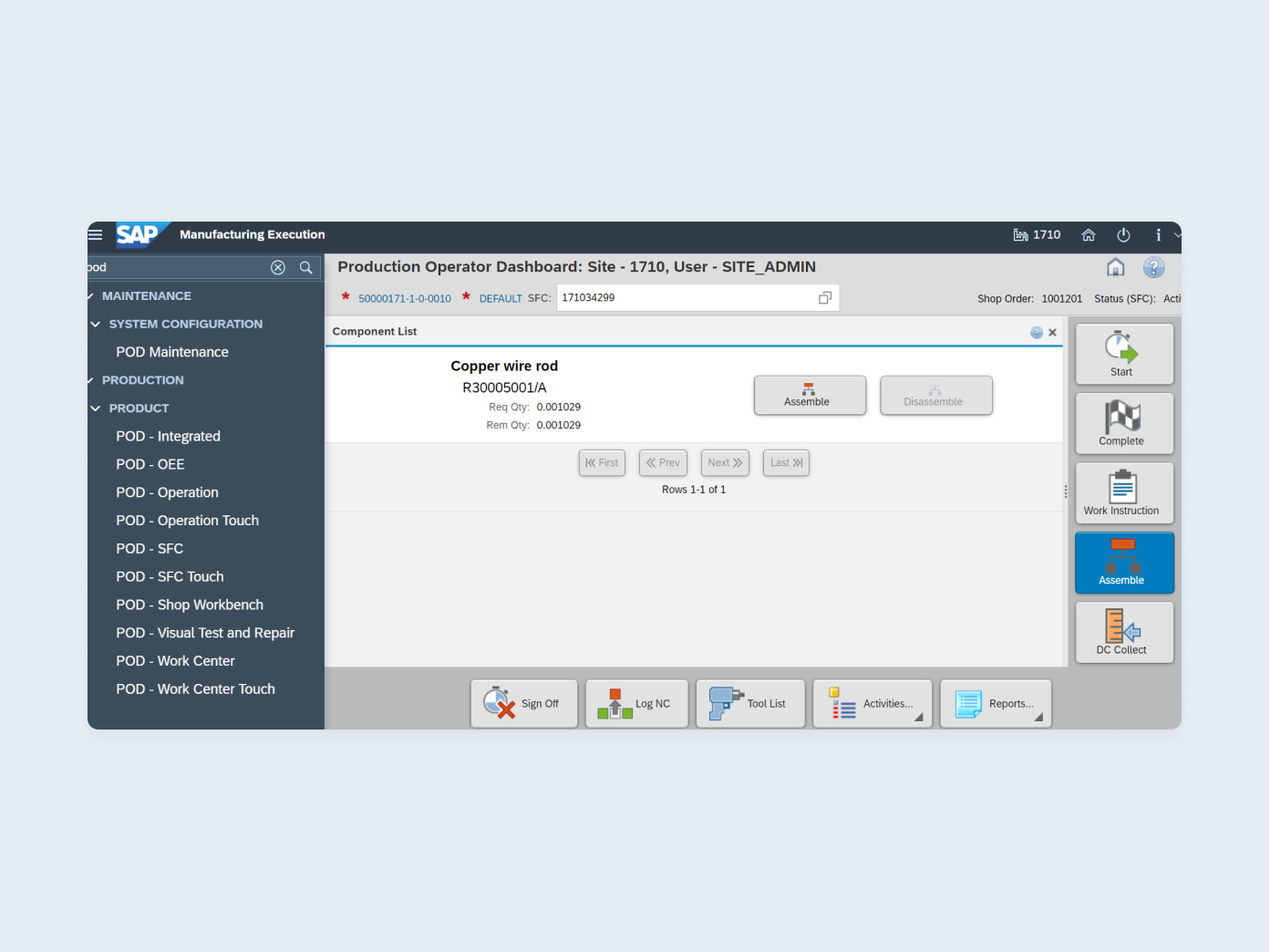
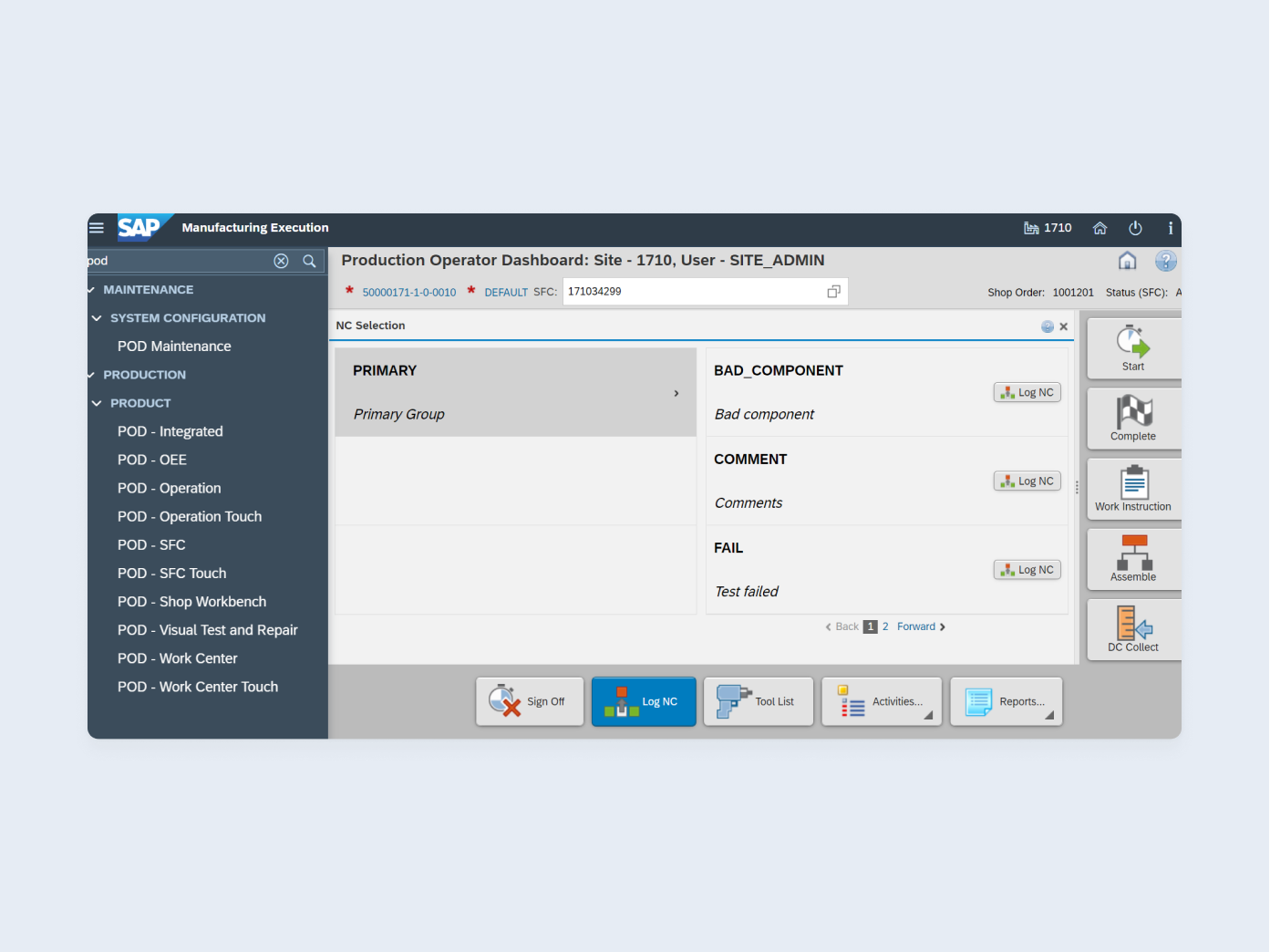
How Can SAP MES Help Your Business?
Unified operations
Live production insights
Traceability and genealogy
Enhanced product quality
Adaptable processes
Equipment and asset oversight
What Business Issues Does MES Address?
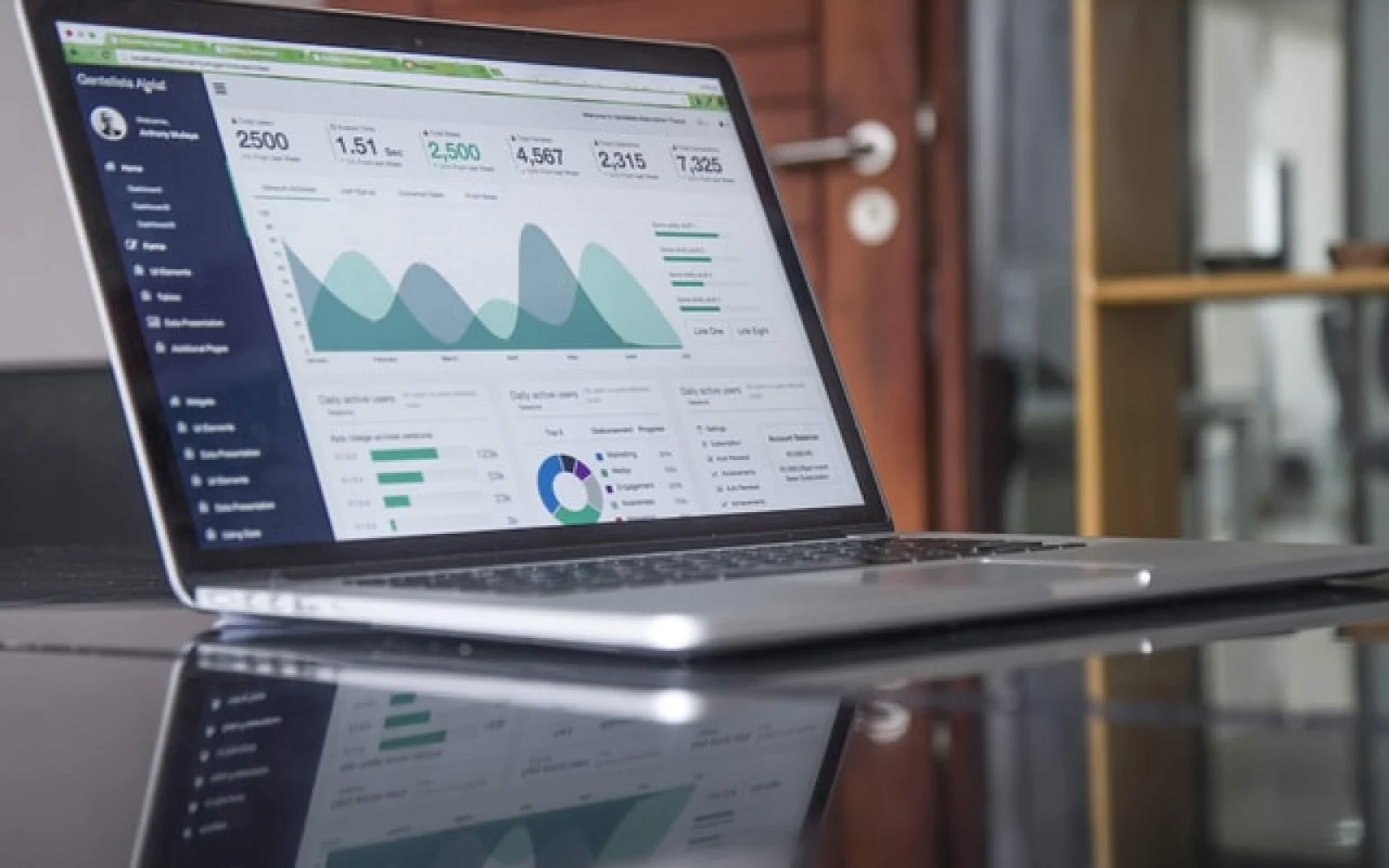
Data collection & visibility
- Monitor and capture real-time production data
- Leverage live reporting tools
- Deliver accurate product data to relevant team members without delay
- View instructions, including in interactive 3D formats
- Gain full visibility into the entire production cycle
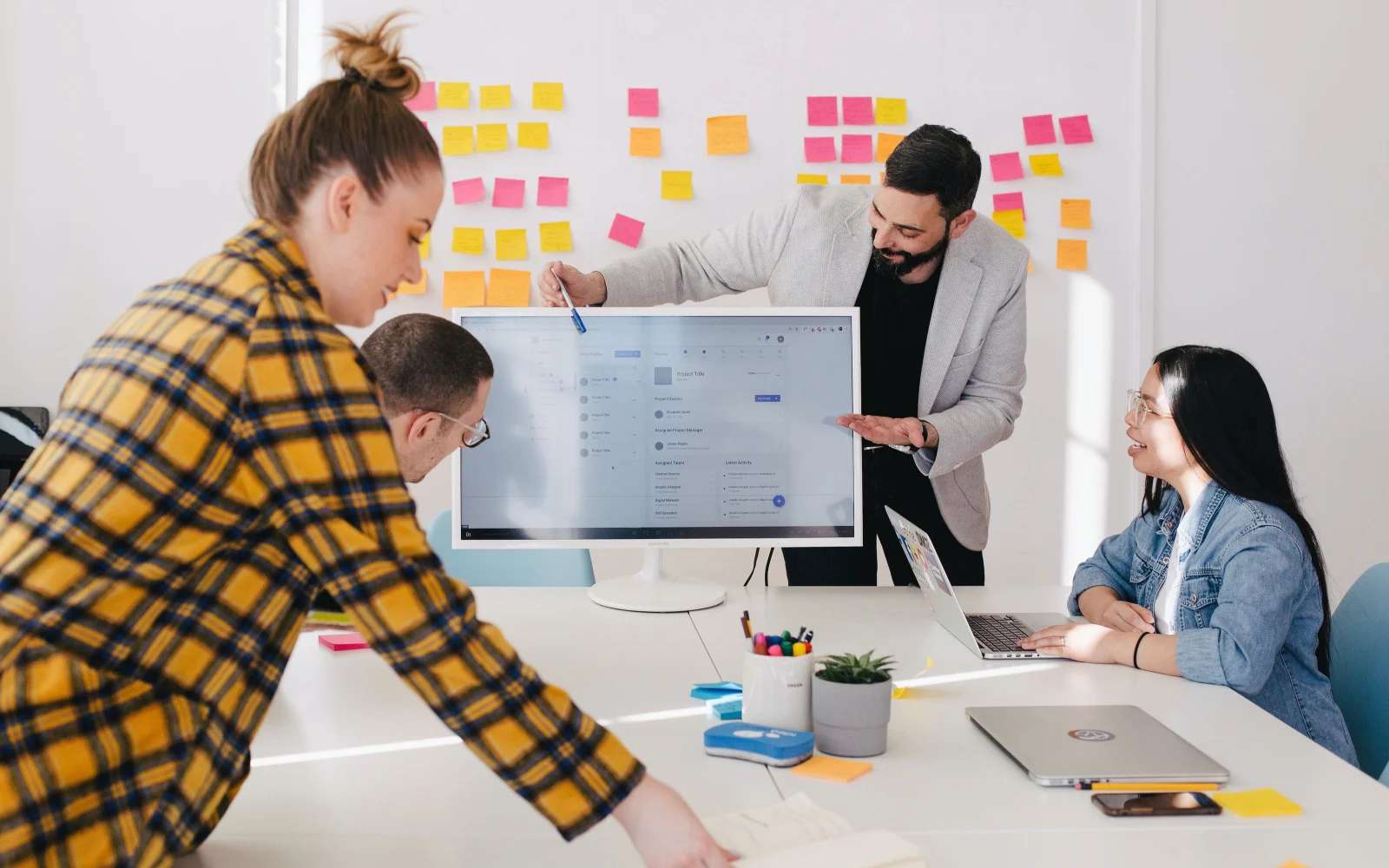
Advanced planning
- Plan production orders efficiently
- Schedule labour and operational tasks
- Manage equipment maintenance schedules
- Optimise capacity planning to meet demand
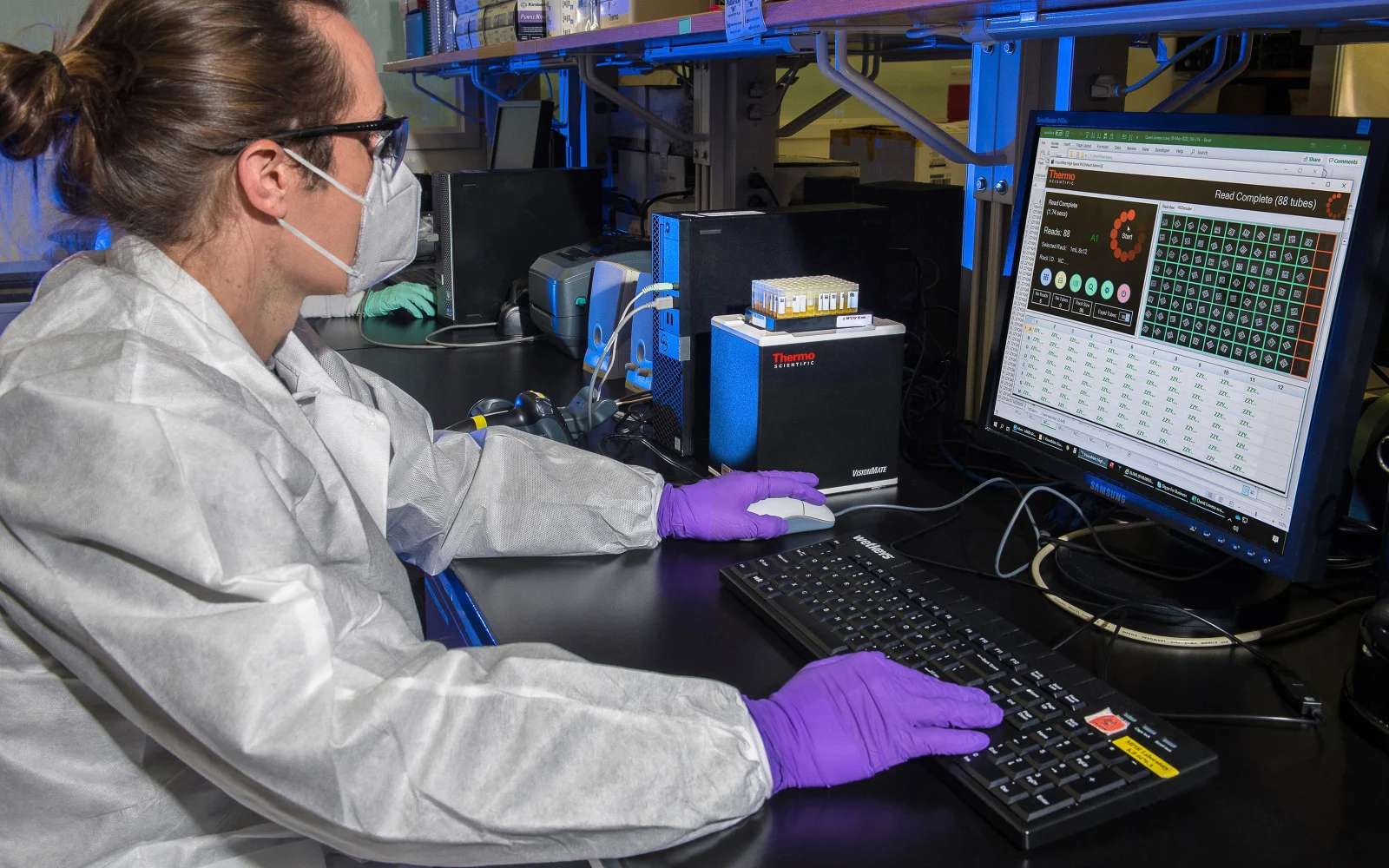
Quality management
- Ensure adherence to product standards
- Identify and respond to quality issues or exceptions
- Oversee quality assurance procedures
- Manage documentation and changes in real time
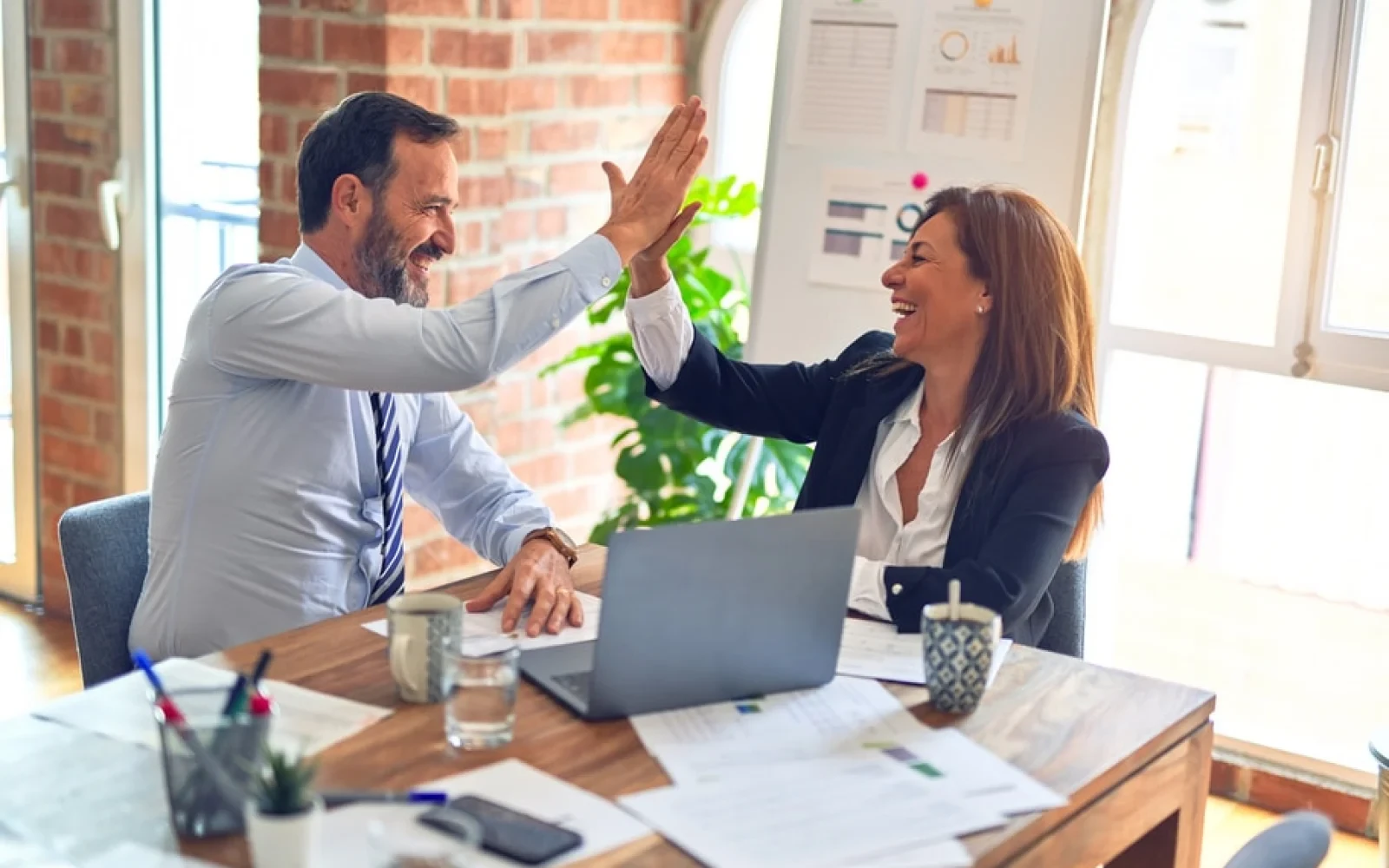
Capacity oversight
- Monitor the effectiveness of production assets
- Visualise current operations on the shop floor
- Maintain control over key production activities
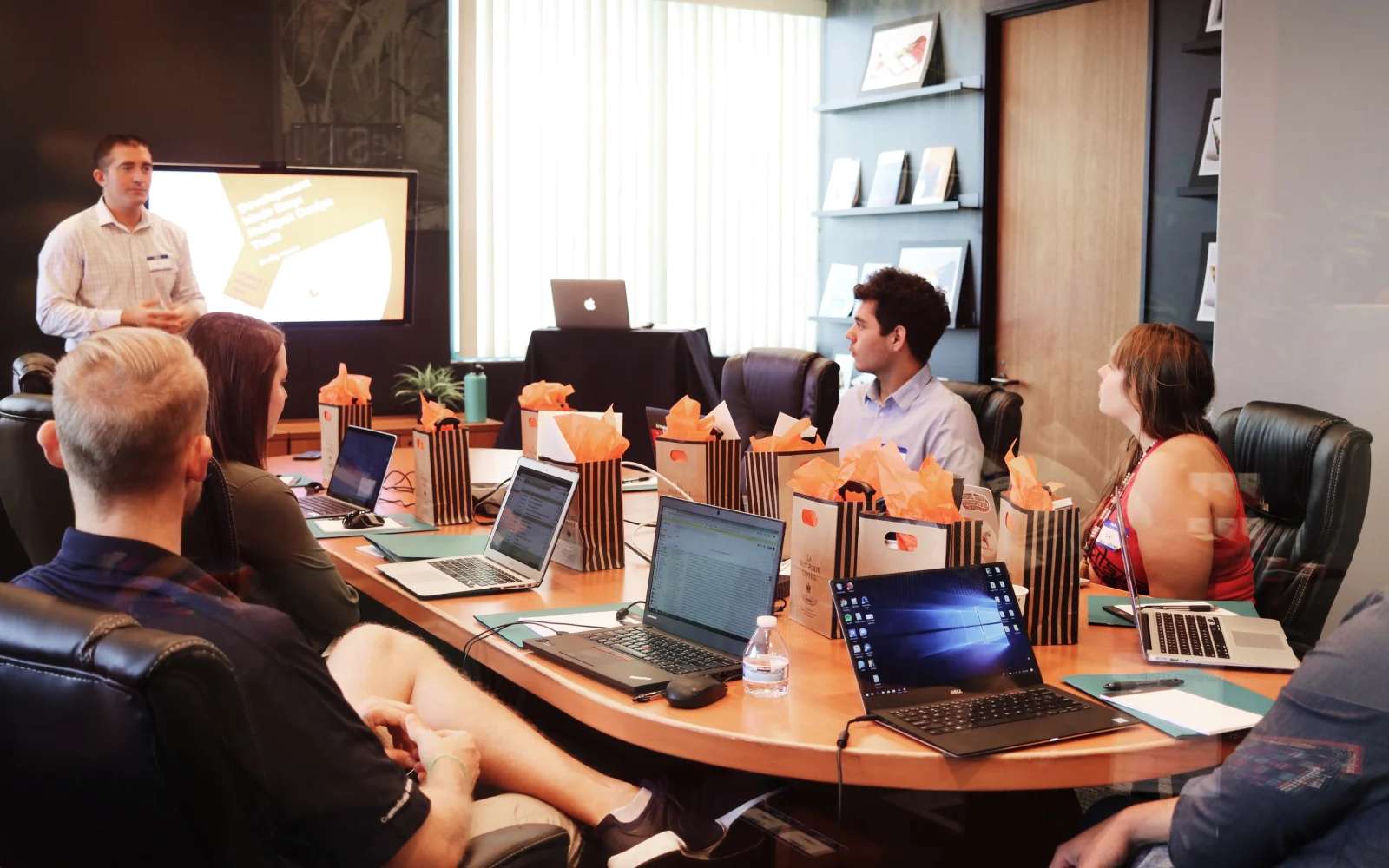
Workforce management
- Track employee skills and qualifications
- Schedule shifts and allocate personnel
- Record and manage staff working hours
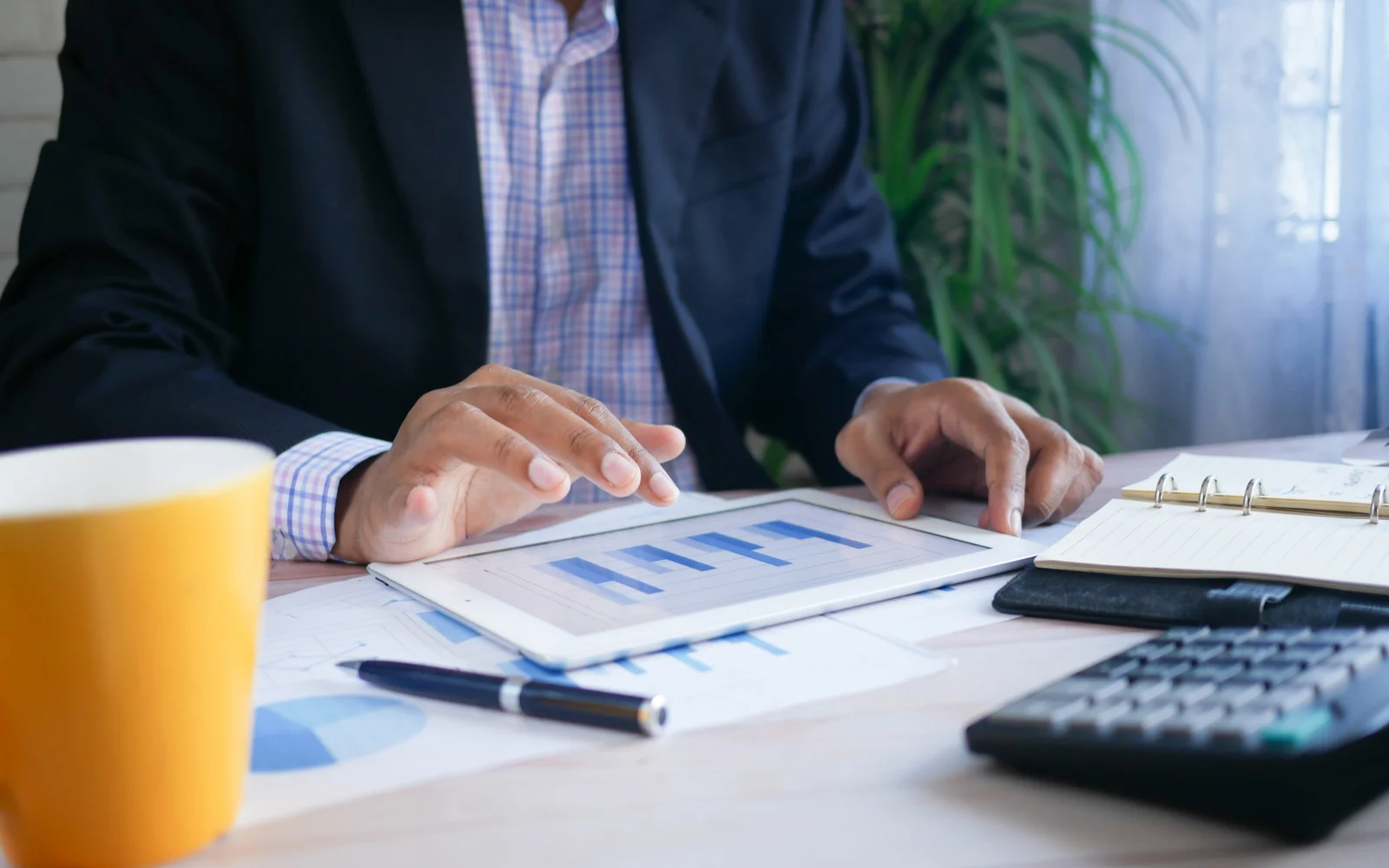
Performance evaluation
- Assess outcomes against targets to uncover strengths and areas for improvement
- Monitor essential KPIs
- Leverage predictive and prescriptive analytics
- Configure alerts and notifications to support decision-making
How Does SAP MES Work?
Operator initiates the order and logs production activities
Components and raw materials are supplied to the production area
Efficient use of production capacities, including machinery and lines
Analysis of collected production data
Enhanced business performance through informed decisions
Growth in profitability
How We Can Help
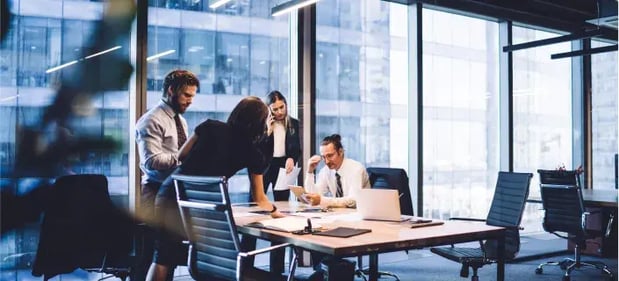
Consulting
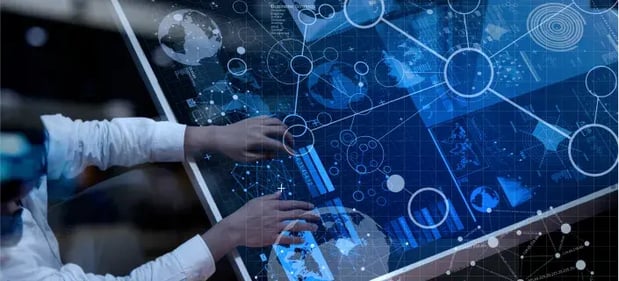
Implementation
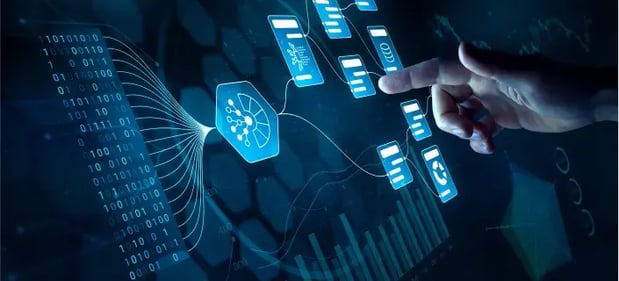
Integration
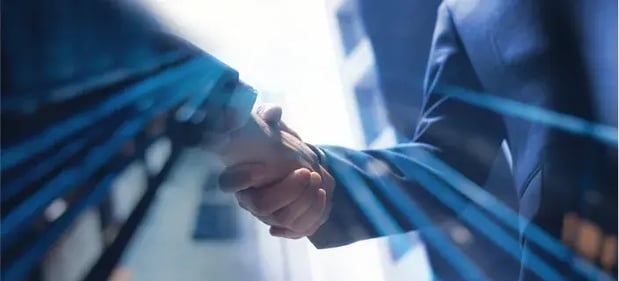
Support
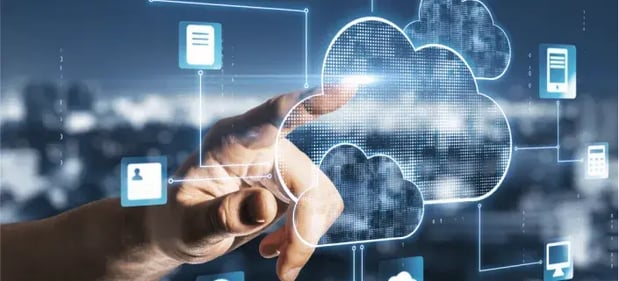
Cloud migration
Customers' success stories
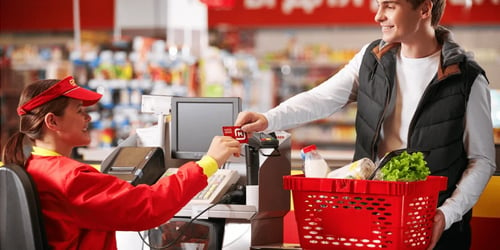
SAP Transportation Management Implementation for a Large Retailer
The LeverX team of experts helped a retail company implement SAP TM, thereby automating transport processes and significantly improving the company's key performance indicators.
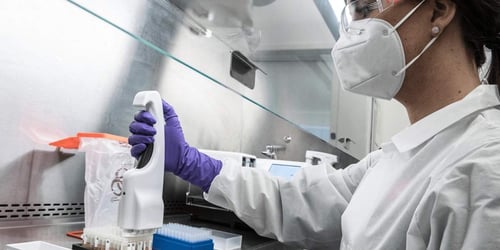
SAP EWM Greenfield Implementation for a Large Manufacturer of Medicines
Thanks to the LeverX team, a customer streamlined warehouse operations and increased material traceability with SAP EWM.
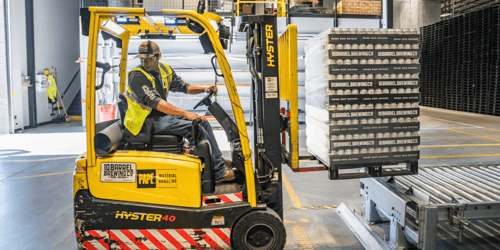
SAP ACM And SAP TSW Integration with SAP TM on SAP S/4HANA for a Manufacturing Provider
Our team was responsible for all integration milestones and the development extensions based on the standard SAP TM objects.
Industries We Serve
Our Partnerships
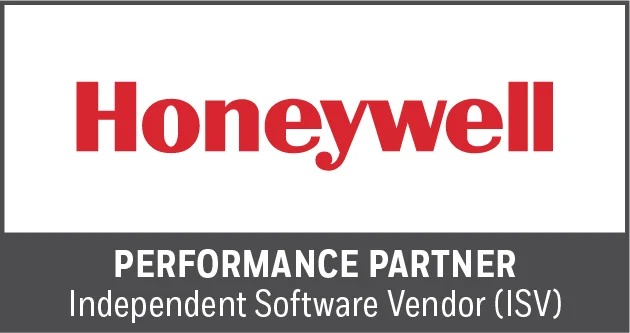
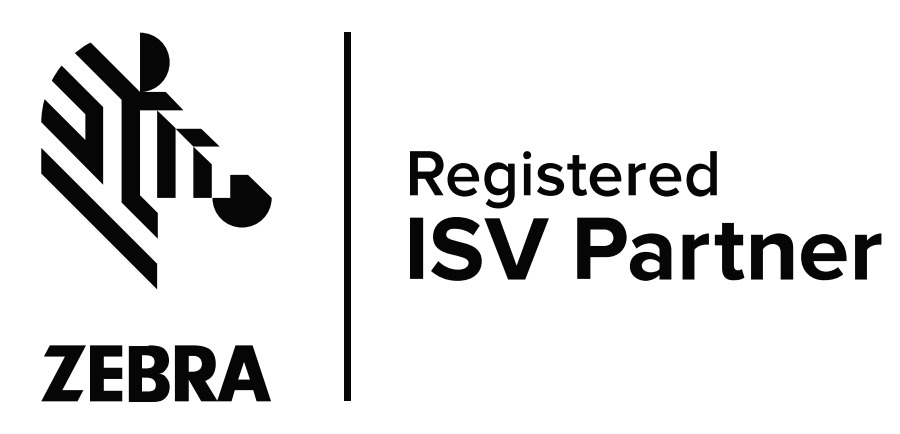
Why Choose LeverX as Your SAP Implementation Provider?
Proven track record
Industry experts
SAP partnership
Quality and security
Investment in innovation
Flexibility
Implementation Roadmap
- Current Processes Evaluation: Assess existing business processes and identify the organization's needs.
- Defining Technical Requirements: Create a detailed specification of the functional and technical needs of the new system.
Discover
- Setting Goals and Objectives: Establish and agree on the goals to be achieved throughout the project.
- Assembling the Project Team: Appoint team members and define their roles and responsibilities.
- Project Plan Development: Create a comprehensive plan that outlines project phases, timelines, resources, and key performance indicators.
- Budget Determination: Estimate and approve the budget.
- Specifications Preparation: Develop the technical and functional specifications for the development team.
Prepare
- Ensuring Business Requirements are Met: Check that SAP MES aligns with business requirements and project objectives.
- Data Validation: Verify the accuracy and compliance of the data.
Explore
- Data Migration: Transfer data from existing systems to the new one.
- System Configuration: Set up the solution according to requirements and specifications.
- Customization: Develop additional features and modules, if the standard solution does not meet all needs.
- Integrations: Configure SAP MES to work with other IT systems and applications.
Realize
- Testing: Perform functional, integration, regression, and load testing to ensure that all works correctly.
- User Training: Organize sessions to help users become familiar with the new system.
Deploy
- System Readiness Check: Verify that the system is ready for operational use.
- Launch: Officially transition to active use of SAP MES.
- Ongoing Support: Continuously monitor solution performance to identify and resolve any issues.
Run
FAQ
How does SAP MES improve production visibility?
Can SAP MES integrate with SAP ERP or SAP S/4HANA?
Can SAP MES help with regulatory compliance?
What industries benefit most from SAP MES?
What is the difference between SAP MII and SAP MES?
Though both are part of SAP’s manufacturing suite, they serve distinct roles. SAP MII acts as a bridge between shop floor equipment and enterprise applications like SAP ERP or S/4HANA, offering tools for data gathering, analysis, and visualisation. In contrast, SAP MES is focused on the execution and oversight of production processes, handling tasks such as order tracking, workforce coordination, and quality assurance.
Can SAP MES enforce standard operating procedures (SOPs) and quality control protocols on the shop floor?
How does SAP MES enhance traceability and genealogy of products, enabling businesses to track raw materials and components throughout the production process?
CONTACT US
If you are looking for an SAP Global Strategic Supplier or Technology Partner for your business, fill out the form below, and we will contact you at short notice.
Contact Us
What happens next?
-
1
An expert will reach out to you to discuss your specific needs and requirements.
-
2
We'll sign an NDA to ensure any sensitive information is kept secure and confidential.
-
3
We'll work with you to prepare a customized proposal based on the project's scope, timeline, and budget.
years of expertise
projects
professionals
Contact Us