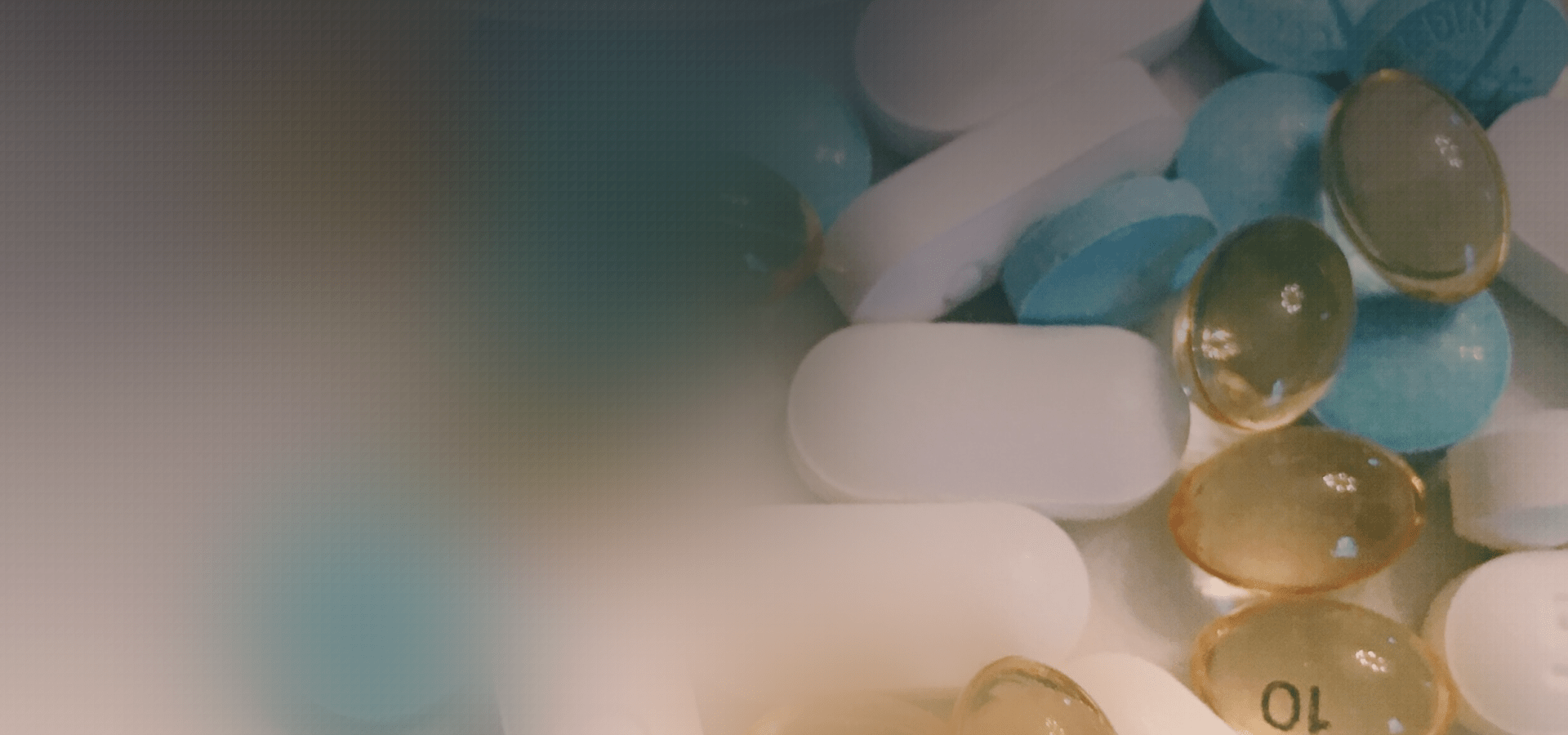
SAP Migration and workflow overhaul for a medical device manufacturer
LeverX migrated all of the company’s processes to SAP and implemented core SAP PLM functions
Table of contents:
LeverX migrated all of the company’s processes to SAP and implemented core SAP PLM functions
Customer
A medical device manufacturing industry leader, representing advanced levels of solid-state liquid and semiconductor technologies.
Challenge
Our customer’s organization was spun off by their parent company, requiring them to establish a new IT infrastructure and migrate from Oracle and Agile to SAP PLM.
Solution
LeverX partnered with another integrator to migrate all of the company’s processes to SAP. We focused on the Product Lifecycle Management (PLM) capabilities and workflow procedures, implementing key quality management processes such as CAPA, SCAR, deviation.
Products and Services
Customer Background
FDA regulations, including compliance with CFR 21 Part 11 requirements, created pressure for accurate record-keeping that would withstand government audits.
Data from multiple systems, including Oracle Agile PLM, needed to be consolidated into one location. It had to be extracted from the legacy systems and transformed for import into SAP. The key challenge was to ensure that proper records and history were imported in the event of audit challenges.
There was a significant learning curve for client employees to understand the nuances of SAP vs their former Oracle and Agile systems. Users were coming from a very mature systems environment with advanced capabilities being added over years of development.
The company desired to consolidate its IT infrastructure into a single ERP system. During discovery, it was determined that the workflows the company wanted could not be supported by SAP base functionality. They needed more flexibility to manage their business processes driven by strict government regulations. Furthermore, the company wanted to continue its operating procedures and practices to maintain consistency.
Project Scope
Core SAP PLM functions
LeverX implemented core SAP PLM functions which included data management processes for materials, Bill of Materials (BOM), document management, engineering changes, material classification, and workflow optimization of key processes.
Quality Management tickets
Quality Management tickets were introduced to address quality monitoring processes. These processes included: corrective action, preventative action tracking, supplier corrective action requests, deviation tickets that allowed some standard deviation for the materials they tracked, health hazard evaluation, and field actions.
IPS integration
LeverX Integrated Process Solution (IPS) integrated the company’s processes, from beginning to end, to address the unique workflows that were required due to regulation, and also gave the company’s end-users the flexibility to make changes on the fly.
BMAX integration
BOM / Material Master Extension & Allocation Tool (BMAX) automated the processes to migrate all of the materials, set up the new Material Master processes, and build extensions in the new ERP.
Velox integration
Velox extracted data from multiple disparate sources and migrated them into the new system.
Cideon Conversion Engine converted all of their paper documentation into pdfs and gave them the ability to approve the final documents.
TOP SAP Company
Results
LeverX successfully centralized multiple disparate systems managing key product data into a single SAP PLM for data and process management. If not for LeverX’s IPS product, the company would still be reliant on manual processes, submitting paper documentation versus electronic documentation. With a good base in place, the company is now moving on to the next phase, which includes enhancements, and additional safeguards to ensure the integrity of the process and reporting/metrics.
More Case Studies
Contact Us
What happens next?
-
1
An expert will reach out to you to discuss your specific needs and requirements.
-
2
We'll sign an NDA to ensure any sensitive information is kept secure and confidential.
-
3
We'll work with you to prepare a customized proposal based on the project's scope, timeline, and budget.
years of expertise
projects
professionals
Contact Us