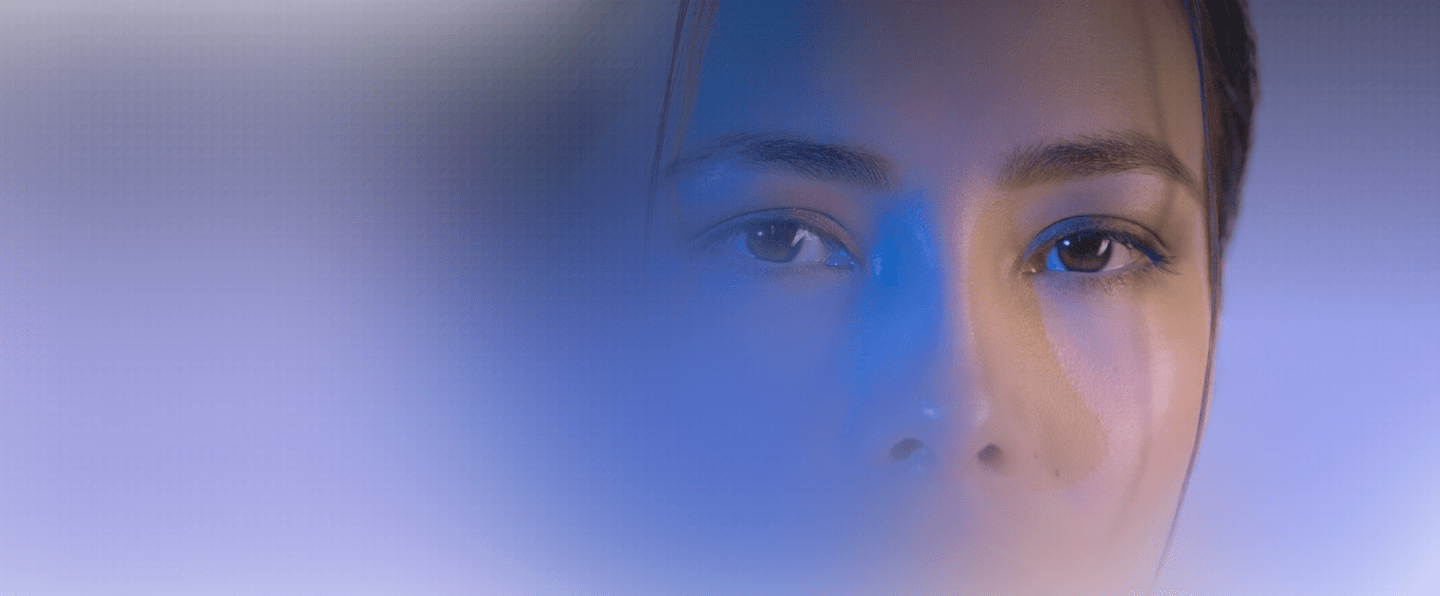
Migration to SAP for a Medical Manufacturer
LeverX assisted a medical device manufacturer migrate to SAP and workflow automation.
Table of contents:
LeverX assisted a medical device manufacturer in migration to SAP and workflow automation.
Customer
The customer is a leading developer and manufacturer of light-based aesthetic and medical treatment systems. The company produces, develops, and manufactures a diverse range of leading treatment applications for hair removal, skin revitalization, scar reduction, gynecological health, body contouring, and more.
Pain
The parent company required the customer to establish a new IT infrastructure and migrate to SAP PLM. Since the company operates in a heavily regulated industry which requires strict control processes and data management, they turned to LeverX for help.
Solution
LeverX partnered with another integrator to migrate all of the company’s processes to SAP. Our team focused on the Engineering Product Lifecycle Management (PLM), and the partner focused on the base ERP system migration.
Products and Services
Challenge
During the transition, data migration was an issue as data from multiple legacy systems had to be extracted and integrated into SAP PLM. There were multiple data touch points missing in their data map documentation, which created holes in their data migration plans. Twenty-five percent of the required data was identified two months prior to the go-live date.
FDA regulations needed to be considered, creating additional pressure for accurate record-keeping that would withstand government audits. The system required added flexibility to accommodate the unique business processes required by the government.
Additionally, there was also a significant learning curve for client employees to understand the nuances of SAP vs their former systems, as they didn’t understand the necessity for the migration.
Key Features
Our specialists implemented core PLM which included: data management processes for materials, Bill of Materials (BOM), document and engineering changes, material classification, and BOM redlining.
Quality Management
Quality Management tickets were introduced to address quality monitoring processes. (Corrective action tracking and preventative action tracking, supplier corrective action requests, deviation tickets that allowed some standard deviation for the materials they tracked, health hazard evaluation, and field actions).
IPS
Integrated Process Solution (IPS) integrated the company’s processes end to end, addressed the unique workflows that were required due to regulation, and also gave the company’s end-users the flexibility to make changes on the fly.
BMAX
BOM / Material Master Extension & Allocation Tool (BMAX) automated the processes to migrate all of their materials, set up the new Material Master processes, and build extensions in the new ERP.
Velox
Velox extracted data from multiple disparate sources and migrated it into the new system.
Cideon Conversion Engine
Cideon Conversion Engine converted all of their paper documentation into pdfs and gave the users the ability to approve them.
Core Technologies
- PLM
- IPS
- BMAX
- VELOX
- CIDEON CONVERSION ENGINE
TOP SAP Company
Results
Our project team successfully centralized multiple disparate systems into a single ERP which eased process management and reduced maintenance and support costs. The new environment enabled the company to move to their phase 2 requirements, opening up additional capabilities that were not possible in their old system, like reporting and business guard rail controls.
The solution increased the company’s flexibility and automated former manual processes within their ERP. If not for LeverX IPS product, the company would still be reliant on manual processes and submitting paper documentation versus submitting documentation electronically.
More Case Studies
Contact Us
What happens next?
-
1
An expert will reach out to you to discuss your specific needs and requirements.
-
2
We'll sign an NDA to ensure any sensitive information is kept secure and confidential.
-
3
We'll work with you to prepare a customized proposal based on the project's scope, timeline, and budget.
years of expertise
projects
professionals
Contact Us