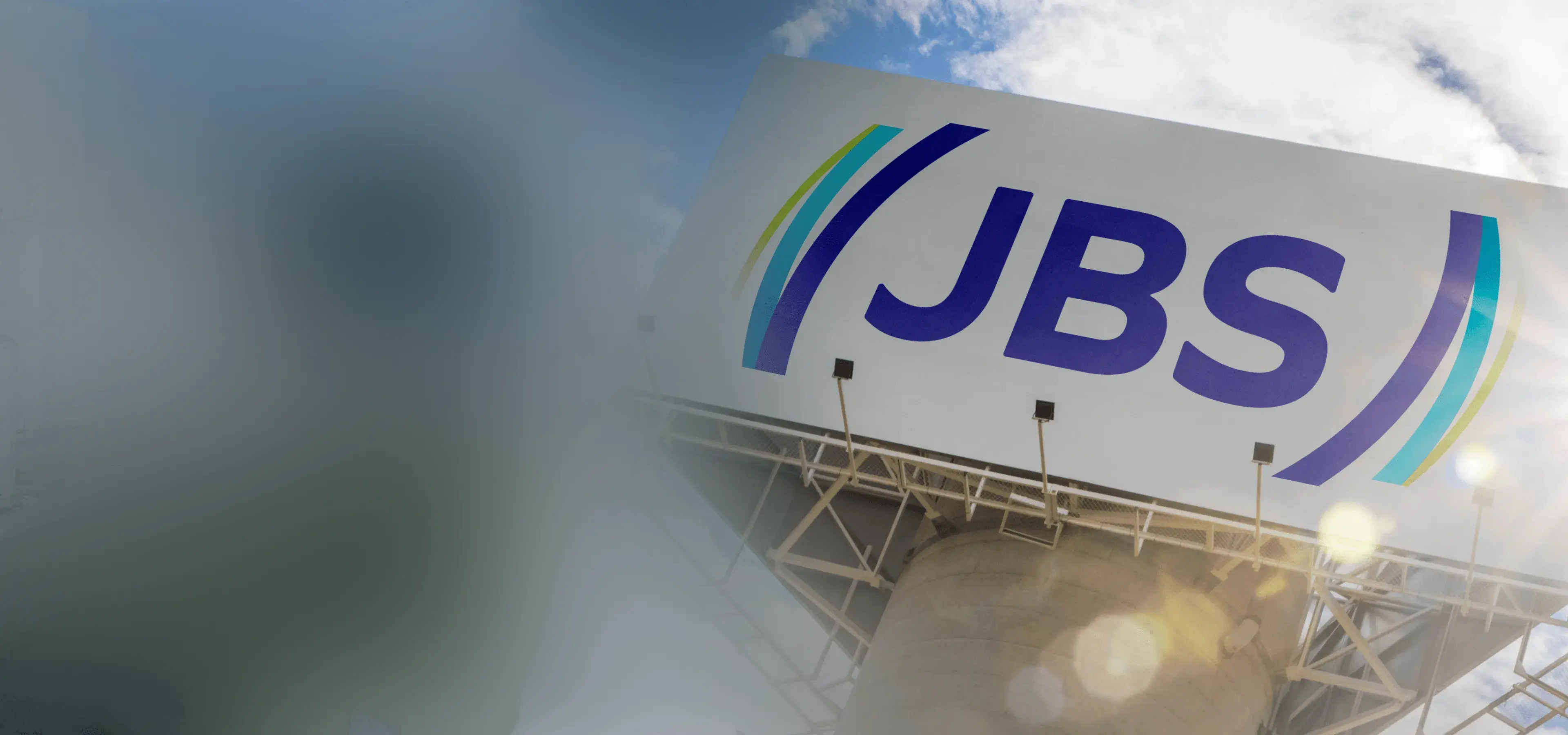
Table of contents:
Our team successfully integrated IPS & BMAX to transform master data creation for a food processing company.
Customer
JBS is a food processing company. One of the world’s leading protein processors with more than 200,000+ team members worldwide, more than 300 production units, and export customers in more than 150 countries. JBS is the largest global producer of beef, chicken, and leather products.
Challenge
The process used for requesting new materials in SAP was disconnected from SAP, putting an unnecessary burden on Master Data Management in vetting requests.
Solution
The LeverX team addressed the business problem by designing a solution using the LeverX Integrated Process Solution (IPS), and BOMS and Material Master Allocation Extension (BMAX) solutions together to automate their process workflows.
Background
- Business users lost time due to rework. Fields were filled out incorrectly, data was missing and data fields had invalid formats.
- Data were collected and stored in SharePoint and then manually entered into SAP. The risk for human error was high. The SharePoint site was on a platform that couldn’t be upgraded due to age. Some requests would get lost in space and not make it into Material Master. Some global business units would email their data. Requests came in from all over the globe in different SharePoint sites and formats.
- The legacy process was overly time-consuming. New materials were needed as soon as possible to allow orders to be placed.
Project Scope
Our team designed a solution using the LeverX Integrated Process Solution (IPS), and BOMS and Material Master Allocation Extension (BMAX) solutions together to automate their process workflows.
BMAX executes the Material Master creation and extension process. Utilize defined rules per the Master data governance guidelines. Material Master rules groups allow for the proper flow and creates/extends the build of the material master.
BMAX Rules: 125 BMAX rules were created
BMAX Groups: 3 rules groups were defined to enable the rules to populate the Material Master
BMAX Populated: The IPS process and BMAX rules populated/extended the data for 18 Material Master views.
TOP SAP Company
The new IPS/BMAX ticket-workflow benefits for the business users
Flexibility and Transparency
- Flexibility for business users to add an additional approver (s) after the ticket is in process. Ad-Hoc
- Greater transparency to the people that process the ticket and the Material
Single Source
- A single source of truth, with all data and processes in SAP
Engagement
- Higher engagement of business groups for reviews and approvals through real-time notifications/processing
Data Governance
- The Material Master data team can now focus on master data governance, which will improve data integrity
Material Request
- Simple and efficient Material request ticket process
Easy Maintain
- The Business has been provided with simple tools that allow them to easily maintain and add/modify workflows. New business units, rules, and workflows can be added, without the need for consulting services.
Increased Demand
- Business users can scale the solution to meet increased demand at will. The volume of Materials this division created was approximately 62,000 annually and this number is expected to increase as the business grows.
Implement and Timing
- The tools implemented will grow as they grow.
- Drastically improved timing. The complete process can be completed in less than 30 minutes from start to finish (now 30 minutes vs 2 days).
Modify
- The business can now modify and add BMAX rules to deploy the solution to the additional business units without the need for consulting services.
Efficient
- Much more efficient and saved 90% of the time in the process.
Products and Services
Business Next-Steps
The business will continue to roll out the process globally to the other thirteen divisions on their timetable. The legacy workflow application will be sunset once the global roll-out is complete. This will allow the current legacy Content Management system (CMS), manual entry process to become obsolete. This will be an organization-wide solution by the end of 2022 and will be transitioned to S/4HANA in Q1 2023.
More Case Studies
Contact Us
What happens next?
-
1
An expert will reach out to you to discuss your specific needs and requirements.
-
2
We'll sign an NDA to ensure any sensitive information is kept secure and confidential.
-
3
We'll work with you to prepare a customized proposal based on the project's scope, timeline, and budget.
years of expertise
projects
professionals
Contact Us